Machining process for flow spoiler bands
A processing technology and a technology of turbulence zone, applied in the field of heat exchanger equipment, can solve the problems of uneven heat exchange, broken sheets, waste products, etc., and achieve the effects of improving cooling effect, large contact area, and increased surface area
- Summary
- Abstract
- Description
- Claims
- Application Information
AI Technical Summary
Problems solved by technology
Method used
Image
Examples
Embodiment Construction
[0020] The present invention will be described in further detail below by means of specific embodiments:
[0021] The reference signs in the accompanying drawings of the specification include: trimming mechanism 1, first base 11, first cutting wheel 12, second cutting wheel 13; heat treatment mechanism 2, second base 21, upper heat conducting roller 22, lower heat conducting roller 23 ; Prefabricated line cutting mechanism 3, the third base 31, beam 32, telescopic cylinder 33, prefabricated line cutting knife 34, the first cutting knife 341, the second cutting knife 342, the third cutting knife 343, the fourth Cutter 344; Torsion mechanism 4, left rotating ring 41, right rotating ring 42, clamping block 43, groove 44, driving gear 45, driven gear 46; air cooling mechanism 5, air cooling pipe 51, communication Pipe 52, prefabricated line A, spoiler unit B.
[0022] The equipment used in the spoiler belt processing technology is basically as attached figure 1 , figure 2 Shown:
PUM
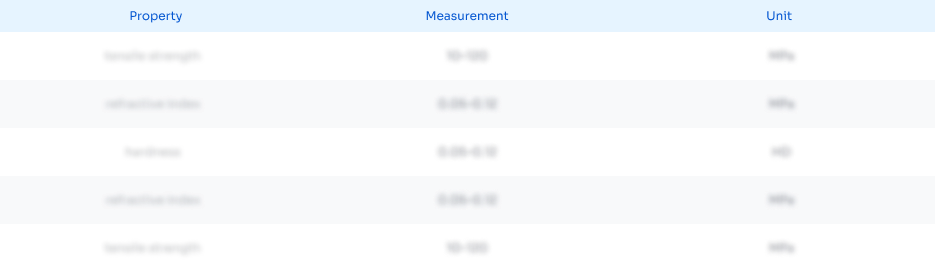
Abstract
Description
Claims
Application Information
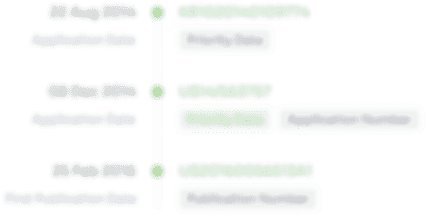
- R&D Engineer
- R&D Manager
- IP Professional
- Industry Leading Data Capabilities
- Powerful AI technology
- Patent DNA Extraction
Browse by: Latest US Patents, China's latest patents, Technical Efficacy Thesaurus, Application Domain, Technology Topic.
© 2024 PatSnap. All rights reserved.Legal|Privacy policy|Modern Slavery Act Transparency Statement|Sitemap