Preparation method of PMI (Polymethacrylimide) foam plastic
A technology of foam plastics and slurry, which is applied in the field of plastic foam profile manufacturing, can solve the problems of high cost and waste of materials, and achieve the effect of improving utilization rate and production efficiency
- Summary
- Abstract
- Description
- Claims
- Application Information
AI Technical Summary
Benefits of technology
Problems solved by technology
Method used
Image
Examples
preparation example Construction
[0025] The invention provides a kind of preparation method of PMI foamed plastics, in this method, the present invention specifically comprises steps:
[0026] S1. Synthesize spare slurry, use methacrylic acid, methacrylonitrile and / or acrylonitrile as monomers for backup, and use C3-C8 alcohols or carbonamide, formamide, diisoamyl phthalate as foam The agent is used for standby, and the high-temperature curing resin or adhesive is used as an additive for standby, and the oil-soluble free radical initiator, monomer, and foaming agent are stirred and mixed at room temperature to make a standby slurry;
[0027] S2. Prepare a foamable copolymer material in a water bath, inject the spare slurry obtained in step 1 into a polymerization mold, and polymerize in a constant temperature water bath to make a foamable copolymer material. In this step, the polymerization mold cavity is used The cuboid structure is designed, so that the foamable copolymer material prepared by the constant te
PUM
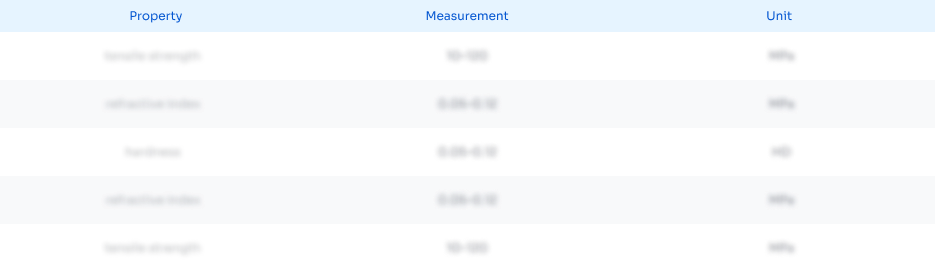
Abstract
Description
Claims
Application Information
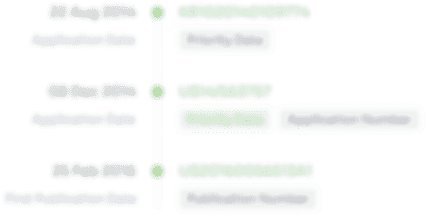
- R&D Engineer
- R&D Manager
- IP Professional
- Industry Leading Data Capabilities
- Powerful AI technology
- Patent DNA Extraction
Browse by: Latest US Patents, China's latest patents, Technical Efficacy Thesaurus, Application Domain, Technology Topic.
© 2024 PatSnap. All rights reserved.Legal|Privacy policy|Modern Slavery Act Transparency Statement|Sitemap