Processing material for stirring paddle of chemical reaction kettle and preparation method of processing material
A technology for processing materials and chemical reactions, applied in chemical instruments and methods, chemical/physical processes, chemical/physical/physical-chemical processes, etc., can solve the problems of coating peeling, corrosion and mottled stirring paddle surface, etc., to reduce replacement costs. , The effect of good formability and excellent corrosion resistance
- Summary
- Abstract
- Description
- Claims
- Application Information
AI Technical Summary
Benefits of technology
Problems solved by technology
Method used
Examples
Embodiment 1
[0023] (1) Add 10 parts of polyvinyl chloride resin and 2 parts of ultrafine polytetrafluoroethylene powder to 20 parts of bisphenol A epoxy resin, heat up to 130-135 ° C at a heating rate of 5 ° C / min and mix for 30 min. Then lower the temperature to 100-105°C at a cooling rate of 5°C / min, add 5 parts of volcanic ash and 1 part of sepiolite fiber, and continue mixing at 100-105°C for 10 minutes to obtain material I;
[0024] (2) Add 5 parts of chlorinated polyvinyl chloride and 2 parts of toughening agent to 15 parts of saturated polyester resin, heat up to 125-130 °C at a heating rate of 5 °C / min and mix for 20 minutes, then add 3 parts of ceramic micropowder , 0.5 part of bistrifluoromethanesulfonimide and 0.5 part of nano rubber powder, and continue to mix at 125-130 ° C for 10 minutes to obtain material II;
[0025] (3) Add 1 part of asbestos powder and 1 part of polyglycerol ricinoleate to material I, after mixing fully, cool down to 0-5 °C at a cooling rate of 5 °C
Embodiment 2
[0029] (1) Add 10 parts of polyvinyl chloride resin and 2 parts of ultrafine polytetrafluoroethylene powder to 20 parts of bisphenol A epoxy resin, heat up to 130-135 ° C at a heating rate of 5 ° C / min and mix for 30 min. Then lower the temperature to 100-105°C at a cooling rate of 5°C / min, add 5 parts of volcanic ash and 1 part of sepiolite fiber, and continue mixing at 100-105°C for 10 minutes to obtain material I;
[0030] (2) Add 5 parts of chlorinated polyvinyl chloride and 3 parts of toughening agent to 15 parts of saturated polyester resin, heat up to 125-130 ° C at a heating rate of 5 ° C / min and mix for 20 minutes, then add 3 parts of ceramic powder , 0.5 parts of bistrifluoromethanesulfonimide and 0.5 parts of nano rubber powder, and continue to mix at 125-130 ° C for 10 minutes to obtain material II;
[0031] (3) Add 2 parts of asbestos powder and 1 part of polyglycerol ricinoleate to material I, after mixing fully, cool down to 0-5 °C at a cooling rate of 5
Embodiment 3
[0035] Utilize the processing material that embodiment 1 and embodiment 2 make to process into the stirring paddle of same size and structure, then install it in the chemical reaction kettle, and its performance is tested.
[0036]The test results show that the impeller can withstand corrosive chemical substances except strong acid and alkali, and can withstand high temperature of 200 ℃, and there will be no surface wear and deformation during the 3-year service life.
PUM
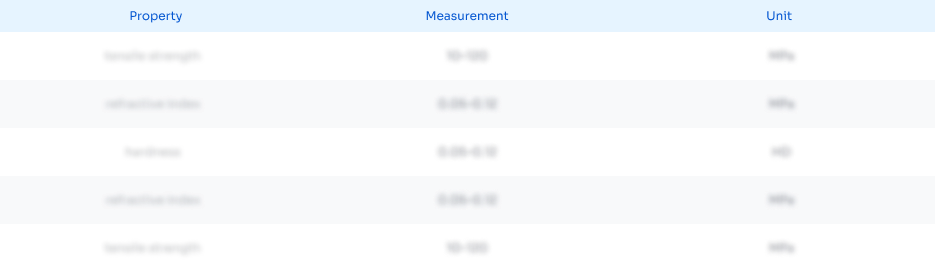
Abstract
Description
Claims
Application Information
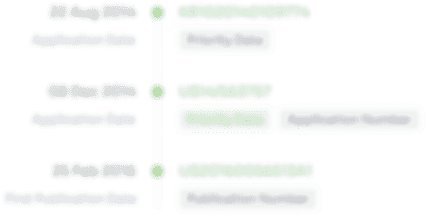
- R&D Engineer
- R&D Manager
- IP Professional
- Industry Leading Data Capabilities
- Powerful AI technology
- Patent DNA Extraction
Browse by: Latest US Patents, China's latest patents, Technical Efficacy Thesaurus, Application Domain, Technology Topic.
© 2024 PatSnap. All rights reserved.Legal|Privacy policy|Modern Slavery Act Transparency Statement|Sitemap