System and method for treating copper-containing molten iron
A technology of molten iron and iron particles, which is applied in transportation and packaging, improvement of process efficiency, metal processing equipment, etc., can solve the problems of difficult large-scale industrial application, inability to further develop, and difficult gas pollution to the environment, and achieves reduction of raw material costs, Low production cost and the effect of improving purity
- Summary
- Abstract
- Description
- Claims
- Application Information
AI Technical Summary
Problems solved by technology
Method used
Image
Examples
Embodiment 1
[0074] Send the copper-containing molten iron at 1450 degrees Celsius to the atomization granulation device for atomization and granulation to obtain copper-containing fine iron particles with a particle size of less than 74 microns, accounting for 86%. Among them, TFe in the copper-containing molten iron contains 95wt%, Cu Containing 1.0wt%; Then the above-mentioned copper-containing fine iron particles, ammonia and carbon dioxide are sent to the stirring leaching tank to carry out ammonia leaching reaction, the ammonia leaching conditions are: the ammonia water mass concentration is 1%, the carbon dioxide mass concentration (in the form of (NH 4 ) 2 CO 3 ) is 2%, the liquid-solid ratio is 10:1, the ammonia immersion temperature is 40 degrees centigrade, and the time is 2h. After the reaction finishes, carry out solid-liquid separation to obtain iron powder and copper-containing ammonia immersion solution. TFe contains 95.5% of the iron powder. wt%, Cu contains 0.05wt%, iron po
Embodiment 2
[0076] Send the copper-containing molten iron at 1500 degrees Celsius to the atomization granulation device for atomization granulation, and obtain copper-containing fine iron particles with a particle size of less than 74 microns, accounting for 90%. Among them, the copper-containing molten iron contains 96wt% TFe and Cu 0.8wt%; then the above-mentioned copper-containing fine iron particles, ammonia and carbon dioxide are sent to the stirring leaching tank to carry out ammonia leaching reaction, and the ammonia leaching conditions are: the ammonia water mass concentration is 3%, and the carbon dioxide mass concentration (in the form of (NH 4 ) 2 CO 3 ) is 4%, the liquid-solid ratio is 6:1, the ammonia immersion temperature is 45 degrees centigrade, and the time is 1h. After the reaction finishes, carry out solid-liquid separation to obtain iron powder and copper-containing ammonia immersion solution. In the iron powder, TFe contains 97.2 wt%, Cu contains 0.04wt%, iron powder ca
Embodiment 3
[0078] Send the copper-containing hot metal at 1525 degrees Celsius to the atomization granulation device for atomization and granulation, and obtain copper-containing fine iron particles with a particle size of less than 74 microns, accounting for 95%. 0.6wt%; then the above-mentioned copper-containing fine iron particles, ammoniacal liquor and carbon dioxide are sent to the stirring leaching tank to carry out ammonia leaching reaction, and the ammonia leaching condition is: the ammoniacal liquor mass concentration is 6%, and the carbon dioxide mass concentration (with (NH 4 ) 2 CO 3 ) is 5%, the liquid-solid ratio is 3:1, the ammonia immersion temperature is 50 degrees Celsius, and the time is 30min. After the reaction is over, solid-liquid separation is carried out to obtain iron powder and copper-containing ammonia immersion solution. TFe content in iron powder is 98.2 wt%, Cu contains 0.03wt%, iron powder can be used as the steelmaking raw material of high-quality carbon st
PUM
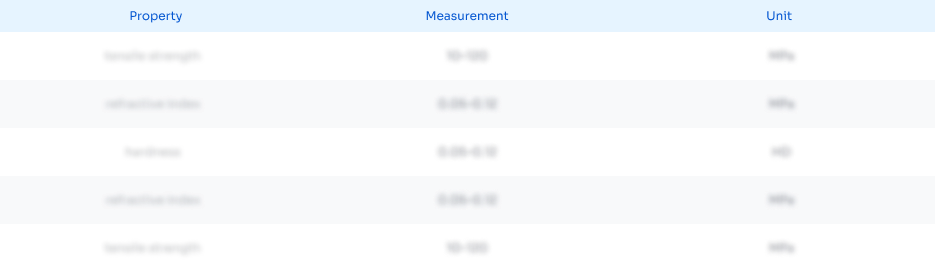
Abstract
Description
Claims
Application Information
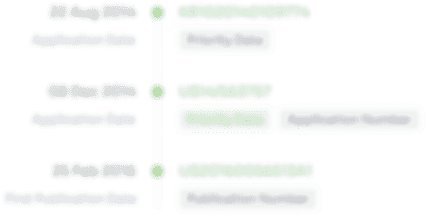
- R&D Engineer
- R&D Manager
- IP Professional
- Industry Leading Data Capabilities
- Powerful AI technology
- Patent DNA Extraction
Browse by: Latest US Patents, China's latest patents, Technical Efficacy Thesaurus, Application Domain, Technology Topic.
© 2024 PatSnap. All rights reserved.Legal|Privacy policy|Modern Slavery Act Transparency Statement|Sitemap