Preparation method for composite material of corrugated pipe of natural gas pipeline
A natural gas pipeline and composite material technology, which is applied in the field of composite material preparation for natural gas pipeline bellows, can solve the problems of easy tearing of the pipe body, reduced elasticity of the stainless steel bellows, poor compressibility of the bellows body, etc., and achieve high Elasticity, good compressibility, high strength effect
- Summary
- Abstract
- Description
- Claims
- Application Information
AI Technical Summary
Benefits of technology
Problems solved by technology
Method used
Examples
Embodiment 1
[0014] ① Take by weight: 70 parts of acrylic rubber, 25 parts of bromobutyl rubber, 10 parts of fluororubber, 6 parts of white carbon black, 15 parts of polytetrafluoroethylene, 8 parts of dioctyl ester, glue T-78 4 parts, 0.5 parts of zinc oxide, 1 part of ferrocene, 2 parts of zinc stearate, 0.3 parts of trilead tetroxide, 3 parts of accelerator TBZTD, and 5 parts of accelerator CZ;
[0015] ② Add zinc oxide, ferrocene, zinc stearate, and lead tetraoxide to grind them into fine powder together with abrasives, then put the resulting mixed fine powder into a microwave oven, heat it for 40 minutes at a power of 200W, take it out and cool it naturally to room temperature;
[0016] ③Add acrylate rubber, bromobutyl rubber, and fluororubber to the internal mixer, and banbury at 85°C for 10 minutes, then continue to add white carbon black, polytetrafluoroethylene, dioctyl ester, and glue T-78, Lower the temperature to 65°C, banbury for 20 minutes, then add the mixed micropowder prepar
Embodiment 2
[0020] ① Take by weight: 80 parts of acrylate rubber, 30 parts of brominated butyl rubber, 15 parts of fluororubber, 10 parts of white carbon black, 18 parts of polytetrafluoroethylene, 12 parts of dioctyl ester, glue T-78 6 parts, 0.8 parts of zinc oxide, 2 parts of ferrocene, 4 parts of zinc stearate, 0.6 parts of trilead tetroxide, 6 parts of accelerator TBZTD, and 8 parts of accelerator CZ;
[0021] ②Add zinc oxide, ferrocene, zinc stearate, and lead tetraoxide to abrasives and grind them into micropowders, then add the resulting mixed micropowders into a microwave oven, heat them at 230W for 50 minutes, take them out and cool them naturally to room temperature;
[0022] ③ Add acrylate rubber, bromobutyl rubber, and fluororubber to the internal mixer, and banbury at 90°C for 15 minutes, then continue to add white carbon black, polytetrafluoroethylene, dioctyl ester, and glue T-78, Lower the temperature to 70°C, banbury for 25 minutes, then add the mixed micropowder prepared
PUM
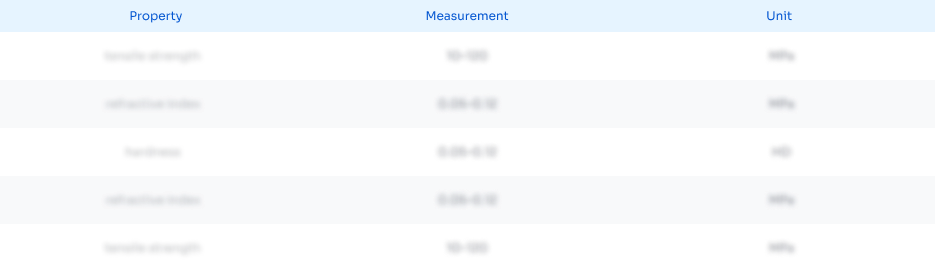
Abstract
Description
Claims
Application Information
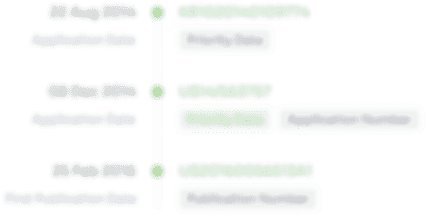
- R&D Engineer
- R&D Manager
- IP Professional
- Industry Leading Data Capabilities
- Powerful AI technology
- Patent DNA Extraction
Browse by: Latest US Patents, China's latest patents, Technical Efficacy Thesaurus, Application Domain, Technology Topic.
© 2024 PatSnap. All rights reserved.Legal|Privacy policy|Modern Slavery Act Transparency Statement|Sitemap