Wear-resistant engineering plastic
A technology of engineering plastics and raw materials, which is applied in the field of wear-resistant engineering plastics, can solve problems such as poor wear resistance, and achieve excellent mechanical properties and remarkable effects
- Summary
- Abstract
- Description
- Claims
- Application Information
AI Technical Summary
Benefits of technology
Problems solved by technology
Method used
Examples
Embodiment 1
[0014] This example is prepared from the following raw materials in parts by weight: 30 parts of polyethylene, 10 parts of polyvinylidene fluoride, 10 parts of polyurethane, 5 parts of phenolic resin, 20 parts of stearic acid, 3 parts of graphite, and 1 part of white carbon black , 2 parts of silicone rubber, 5 parts of EPDM rubber, 0.5 part of nano-zirconia with a particle diameter of 0 nanometers, 0.5 part of nano-titanium dioxide, and 1 part of glass fiber with a diameter of 20 microns; wherein, the relative molecular weight of polyethylene is greater than 3.2 million.
Embodiment 2
[0016] This example is prepared from the following raw materials in parts by weight: 20 parts of polyethylene, 17 parts of polyvinylidene fluoride, 15 parts of polyurethane, 9 parts of phenolic resin, 10 parts of stearic acid, 7 parts of graphite, and 5 parts of white carbon black , 7 parts of silicone rubber, 10 parts of EPDM rubber, 3 parts of nano-zirconia with a particle diameter of 60 nanometers, 2 parts of nano-titanium dioxide, and 3 parts of glass fibers with a diameter of 15 microns; wherein, the relative molecular weight of polyethylene is greater than 3.2 million.
Embodiment 3
[0018] This example is prepared from the following raw materials in parts by weight: 40 parts of polyethylene, 25 parts of polyvinylidene fluoride, 20 parts of polyurethane, 12 parts of phenolic resin, 15 parts of stearic acid, 10 parts of graphite, and 3 parts of white carbon black , 10 parts of silicone rubber, 15 parts of EPDM rubber, 5 parts of nano-zirconia with a particle diameter of 80 nanometers, 3 parts of nano-titanium dioxide, and 6 parts of glass fibers with a diameter of 10 microns; wherein, the relative molecular weight of polyethylene is greater than 3.2 million.
PUM
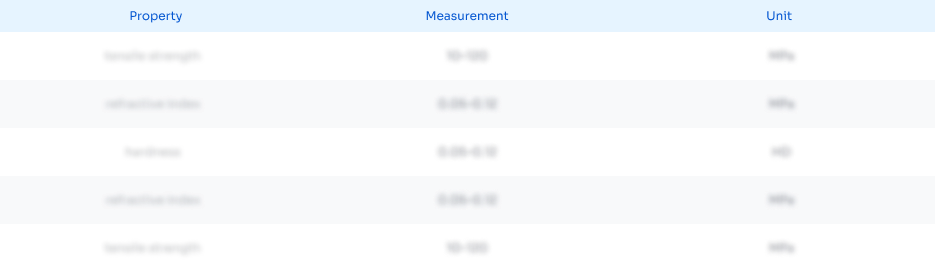
Abstract
Description
Claims
Application Information
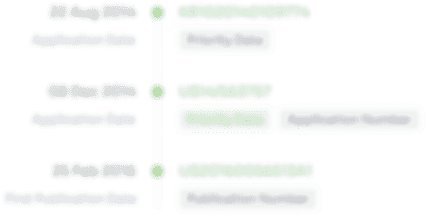
- R&D Engineer
- R&D Manager
- IP Professional
- Industry Leading Data Capabilities
- Powerful AI technology
- Patent DNA Extraction
Browse by: Latest US Patents, China's latest patents, Technical Efficacy Thesaurus, Application Domain, Technology Topic.
© 2024 PatSnap. All rights reserved.Legal|Privacy policy|Modern Slavery Act Transparency Statement|Sitemap