Foamed concrete material and preparation method thereof
A technology of foam concrete and raw materials, applied in the field of construction, can solve the problems of high pollution in cement production and transportation, high production cost of plates, and high thermal conductivity, and achieve the effects of low production cost, reduced cost, and low thermal conductivity
- Summary
- Abstract
- Description
- Claims
- Application Information
AI Technical Summary
Problems solved by technology
Method used
Examples
Embodiment 1
[0021] A foam concrete material, comprising the following raw materials in parts by weight: 30 parts of mountain mud, 20 parts of field soil, 10 parts of illite, 10 parts of coal gangue slag, 15 parts of sugarcane waste slag, 1 part of zirconium, 3 parts of polymethylacrylate, 2 parts of expanded graphite, 4 parts of paraffin wax, 3 parts of magnesium stearate, 2 parts of sodium tripolyphosphate, 2 parts of tobacco leaf powder, and 0.5 part of foaming agent.
[0022] A preparation method of a foamed concrete material, the preparation steps are:
[0023] (1) Mix mountain mud, field soil, illite, zirconium, coal gangue slag and sugarcane waste slag, dry at 75°C for 25 minutes, crush with a crusher, and sieve through 200 mesh;
[0024] (2) Mix polymethyl acrylate, expanded graphite, paraffin, magnesium stearate, tobacco leaf powder and sodium tripolyphosphate, stir at 80°C for 25 minutes, and the stirring speed is 115 rpm;
[0025] (3) Mix the product of step (1), the product of st
Embodiment 2
[0030] A foam concrete material, comprising the following raw materials in parts by weight: 45 parts of mountain mud, 32 parts of field soil, 20 parts of illite, 18 parts of coal gangue slag, 22 parts of sugarcane waste slag, 3 parts of zirconium, 8 parts of polymethylacrylate, 8 parts of expanded graphite, 9 parts of paraffin wax, 6 parts of magnesium stearate, 6 parts of sodium tripolyphosphate, 8 parts of tobacco leaf powder, and 2 parts of foaming agent.
[0031] A preparation method of a foamed concrete material, the preparation steps are:
[0032] (1) Mix landslide, field soil, illite, zirconium, coal gangue slag and sugarcane waste slag, dry at 89°C for 40 minutes, crush with a crusher, and sieve through 300 mesh;
[0033] (2) Mix polymethyl acrylate, expanded graphite, paraffin, magnesium stearate, tobacco leaf powder and sodium tripolyphosphate, stir at 95°C for 55min, and stir at a speed of 200 rpm;
[0034] (3) Mix the product of step (1), the product of step (2) and
Embodiment 3
[0039] A foam concrete material, comprising the following raw materials in parts by weight: 42 parts of mountain mud, 29 parts of field soil, 16 parts of illite, 15 parts of coal gangue slag, 20 parts of sugarcane waste slag, 2 parts of zirconium, 6 parts of polymethylacrylate, 3 parts of expanded graphite, 5 parts of paraffin wax, 4 parts of magnesium stearate, 5.5 parts of sodium tripolyphosphate, 6 parts of tobacco leaf powder, and 1 part of foaming agent.
[0040] A preparation method of a foamed concrete material, the preparation steps are:
[0041] (1) Mix landslide, field soil, illite, zirconium, coal gangue slag and sugarcane waste slag, dry at 82°C for 30 minutes, crush with a crusher, and sieve through a 250-mesh sieve.
[0042] (2) Mix polymethyl acrylate, expanded graphite, paraffin, magnesium stearate, tobacco leaf powder and sodium tripolyphosphate, and stir for 40 minutes at 85° C. at a stirring speed of 165 rpm.
[0043] (3) Mix the product of step (1), the produ
PUM
Property | Measurement | Unit |
---|---|---|
Compressive strength | aaaaa | aaaaa |
Thermal conductivity | aaaaa | aaaaa |
Compressive strength | aaaaa | aaaaa |
Abstract
Description
Claims
Application Information
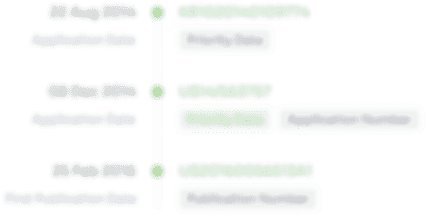
- R&D Engineer
- R&D Manager
- IP Professional
- Industry Leading Data Capabilities
- Powerful AI technology
- Patent DNA Extraction
Browse by: Latest US Patents, China's latest patents, Technical Efficacy Thesaurus, Application Domain, Technology Topic.
© 2024 PatSnap. All rights reserved.Legal|Privacy policy|Modern Slavery Act Transparency Statement|Sitemap