Acrylic resin for water-borne wood paint finishing coat and preparation method of acrylic resin
A water-based wood lacquer and acrylic resin technology, applied in the field of wood lacquer, can solve the problems affecting the promotion and use of water-based wood lacquer, the fullness cannot meet people's requirements, and the environmental protection standards are not met. Good salt spray resistance
- Summary
- Abstract
- Description
- Claims
- Application Information
AI Technical Summary
Benefits of technology
Problems solved by technology
Method used
Examples
Embodiment 1
[0027] A kind of acrylic resin for water-based wood finish paint, which is mainly prepared from the following raw materials: methacrylic acid 144g, methyl methacrylate 90g, n-butyl methacrylate 135g, isobornyl methacrylate 180g, methacrylic acid 90 g of 2-hydroxypropyl acrylate, 270 g of cycloaliphatic acrylate, 18 g of initiator, 100 g of 3-methacryloxytriisopropoxysilane and vinyltrimethoxysilane, and 106 g of prepolymer.
[0028] The initiator is a mixture of benzoyl peroxide and di-tert-amyl peroxide.
[0029] A kind of acrylic resin preparation process for water-based wood finish paint is as follows:
[0030] ① Mix n-butyl methacrylate, isobornyl methacrylate, 2-hydroxypropyl methacrylate, cycloaliphatic acrylate and 12g initiator, and dissolve them evenly for later use;
[0031] ②Mix methacrylic acid, methyl methacrylate and 6g initiator, and dissolve them evenly for later use;
[0032] ③Put 810g of toluene into the reaction kettle, heat it to reflux and maintain reflux,
Embodiment 2
[0035] A kind of acrylic resin for water-based wood finish paint, which is mainly prepared from the following raw materials: 135g of methacrylic acid, 90g of methyl methacrylate, 144g of n-butyl methacrylate, 180g of isobornyl methacrylate, methacrylic acid 90 g of 2-hydroxypropyl acrylate, 270 g of alicyclic acrylate, 20 g of an initiator, 100 g of triethoxypropyl acrylate, and 106 g of a prepolymer.
[0036] The initiator is a mixture of benzoyl peroxide and di-tert-amyl peroxide.
[0037] A kind of acrylic resin preparation process for water-based wood finish paint is as follows:
[0038] ①Mix n-butyl methacrylate, isobornyl methacrylate, 2-hydroxypropyl methacrylate, cycloaliphatic acrylate and 14g initiator, and dissolve them evenly for later use;
[0039] ②Mix methacrylic acid, methyl methacrylate and 6g initiator, and dissolve them evenly for later use;
[0040] ③Put 810g of toluene into the reaction kettle, heat it to reflux and maintain reflux, start to drop the mixtur
Embodiment 3
[0043] A kind of acrylic resin for water-based wood finish paint, which is mainly prepared from the following raw materials: 180g of methacrylic acid, 144g of methyl methacrylate, 90g of n-butyl methacrylate, 135g of isobornyl methacrylate, methacrylic acid 90 g of 2-hydroxypropyl acrylate, 270 g of alicyclic acrylate, 19 g of an initiator, 100 g of 3-methacryloyloxytriisopropoxysilane, and 106 g of a prepolymer.
[0044] The initiator is a mixture of benzoyl peroxide and di-tert-amyl peroxide.
[0045] A kind of acrylic resin preparation process for water-based wood finish paint is as follows:
[0046] ①Mix n-butyl methacrylate, isobornyl methacrylate, 2-hydroxypropyl methacrylate, cycloaliphatic acrylate and 14g initiator, and dissolve them evenly for later use;
[0047]②Mix methacrylic acid, methyl methacrylate and 5g initiator, and dissolve them evenly for later use;
[0048] ③Put 810g of toluene into the reaction kettle, heat it to reflux and maintain reflux, start to drop
PUM
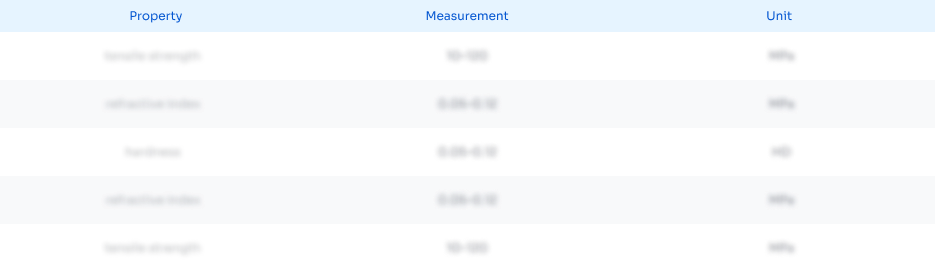
Abstract
Description
Claims
Application Information
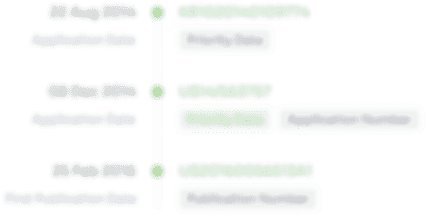
- R&D Engineer
- R&D Manager
- IP Professional
- Industry Leading Data Capabilities
- Powerful AI technology
- Patent DNA Extraction
Browse by: Latest US Patents, China's latest patents, Technical Efficacy Thesaurus, Application Domain, Technology Topic.
© 2024 PatSnap. All rights reserved.Legal|Privacy policy|Modern Slavery Act Transparency Statement|Sitemap