Wear-resistant non-toxic modified plastic production method
A production process and plastic technology, which is applied in the field of wear-resistant and non-toxic modified plastic production process, can solve the problems of poor wear resistance, dust sticking, non-environmental protection, etc., achieve good thermal performance, good toughness, and improve wear resistance Effect
- Summary
- Abstract
- Description
- Claims
- Application Information
AI Technical Summary
Problems solved by technology
Method used
Examples
Embodiment 1
[0021] A production process of wear-resistant and non-toxic modified plastics, the specific steps of the production process of wear-resistant and non-toxic modified plastics are as follows:
[0022] S1. Ingredients: Weigh 40 parts of polypropylene, 30 parts of polyvinyl chloride, 25 parts of glass fiber, 15 parts of carbon fiber, 1 part of coupling agent, 10 parts of polytetrafluoroethylene, 0.5 parts of lubricant and 5 parts of low-density polyethylene ;
[0023] S2, material mixing: add the material weighed by S1 into the mixer to fully mix and grind, put it into the vacuum mixer after mixing and grind for 5 minutes, so that the mixture in S1 is fully mixed;
[0024] S3. Extrusion: put the fully mixed material in S2 into a twin-screw extruder to extrude. The temperature of the twin-screw extruder is kept at 180°C, and the speed of the screw is 280r / min. After extrusion, the injection molding temperature 160°C;
[0025] S4. Cooling: Place the injection-molded plastic in S3 i
Embodiment 2
[0034] A production process of wear-resistant and non-toxic modified plastics, the specific steps of the production process of wear-resistant and non-toxic modified plastics are as follows:
[0035] S1. Ingredients: Weigh 42 parts of polypropylene, 32 parts of polyvinyl chloride, 27 parts of glass fiber, 18 parts of carbon fiber, 1.25 parts of coupling agent, 12 parts of polytetrafluoroethylene, 0.7 parts of lubricant and 6 parts of low-density polyethylene ;
[0036] S2, material mixing: add the material weighed by S1 into the mixer to fully mix and grind, put it into the vacuum mixer after mixing and grind for 5 minutes, so that the mixture in S1 is fully mixed;
[0037] S3. Extrusion: Put the fully mixed material in S2 into a twin-screw extruder to extrude. The temperature of the twin-screw extruder is kept at 200°C, and the speed of the screw is 280r / min. After extrusion, the injection molding temperature 170°C;
[0038] S4. Cooling: Place the injection-molded plastic in
Embodiment 3
[0047] A production process of wear-resistant and non-toxic modified plastics, the specific steps of the production process of wear-resistant and non-toxic modified plastics are as follows:
[0048] S1. Ingredients: Weigh 45 parts of polypropylene, 35 parts of polyvinyl chloride, 30 parts of glass fiber, 20 parts of carbon fiber, 1.5 parts of coupling agent, 15 parts of polytetrafluoroethylene, 1 part of lubricant and 7 parts of low-density polyethylene ;
[0049] S2, material mixing: add the material weighed by S1 into the mixer to fully mix and grind, put it into the vacuum mixer after mixing and grind for 5 minutes, so that the mixture in S1 is fully mixed;
[0050] S3. Extrusion: Put the fully mixed material in S2 into a twin-screw extruder to extrude. The temperature of the twin-screw extruder is kept at 220°C, and the speed of the screw is 280r / min. After extrusion, the injection molding temperature 180°C;
[0051] S4. Cooling: Place the injection-molded plastic in S3 i
PUM
Property | Measurement | Unit |
---|---|---|
Length | aaaaa | aaaaa |
Density | aaaaa | aaaaa |
Abstract
Description
Claims
Application Information
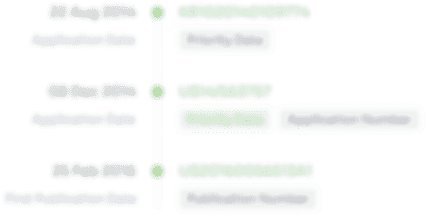
- R&D Engineer
- R&D Manager
- IP Professional
- Industry Leading Data Capabilities
- Powerful AI technology
- Patent DNA Extraction
Browse by: Latest US Patents, China's latest patents, Technical Efficacy Thesaurus, Application Domain, Technology Topic.
© 2024 PatSnap. All rights reserved.Legal|Privacy policy|Modern Slavery Act Transparency Statement|Sitemap