Ceramsite petroleum fracturing propping agent and preparation method thereof
A fracturing proppant and oil technology, which is applied in chemical instruments and methods, earth-moving drilling and production of fluids, etc., can solve the problems of easy settlement, difficult to transport proppant, unable to achieve ideal oil and gas stimulation effect, etc., to improve the strength , the effect of promoting growth
- Summary
- Abstract
- Description
- Claims
- Application Information
AI Technical Summary
Problems solved by technology
Method used
Examples
Example Embodiment
[0022] Example 1
[0023] Take the kaolin into a pulverizer and pulverize, pass a 100-mesh sieve, place the sieved kaolin powder in a muffle furnace, heat it to 800°C, heat it for 1 hour, and obtain pretreated kaolin. Take 60g pretreated kaolin, 1g Manganese oxide, 1g dolomite, 4g anorthite, 1g vanadium pentoxide, pulverize in a pulverizer, pass through a 200-mesh sieve, add the sieved powder to a planetary ball mill, and use anhydrous ethanol as the ball milling medium for ball milling for 10 hours , Take out the slurry and place it in a drying box, dry to constant weight at 105°C to obtain composite powder, take 1g polyvinyl alcohol into 10mL deionized water, heat to 90°C, stir at 300r / min for 30min, and then add 5g of urea, continue to stir for 20 minutes and then drip into the composite powder at 1mL / min to mix evenly, then transfer to the granulator to granulate, sieve out particles with a particle size of 0.8mm to obtain spherical pellets, and place the pellets Dry it in
Example Embodiment
[0024] Example 2
[0025] Take the kaolin into a pulverizer and pulverize, pass a 100-mesh sieve, place the sieved kaolin powder in a muffle furnace, heat it to 850°C, heat it for 1 hour, and obtain pretreated kaolin. Take 65g pretreated kaolin, 3g Manganese oxide, 1g dolomite, 6g anorthite, 1g vanadium pentoxide, pulverized in a pulverizer, sieved through a 200-mesh sieve, the sieved powder is added to the planetary ball mill, and anhydrous ethanol is used as the ball milling medium for ball milling for 11 hours , Take out the slurry and place it in a drying box, dry to constant weight at 108℃, to obtain composite powder, take 1g polyvinyl alcohol into 15mL deionized water, heat to 92℃, stir at 350r / min for 35min, and then add 8g of urea, continue to stir for 25 minutes, and then drip into the composite powder at 1mL / min to mix evenly, then transfer to the granulator to granulate, sieve out the particles with a particle size of 0.9mm to obtain spherical pellets, and place the p
Example Embodiment
[0026] Example 3
[0027] Take the kaolin into a pulverizer and pulverize, pass a 100-mesh sieve, and place the sieved kaolin powder in a muffle furnace, heat it to 900°C, heat it for 2 hours, and obtain pretreated kaolin. Take 70g pretreated kaolin, 5g 2 Manganese oxide, 2g dolomite, 8g anorthite, 2g vanadium pentoxide, pulverize in a pulverizer, pass a 200-mesh sieve, add the sieved powder to a planetary ball mill, and use anhydrous ethanol as a ball milling medium to mill for 12 hours , Take out the slurry and place it in a drying box, dry to constant weight at 110°C to obtain composite powder, take 2g polyvinyl alcohol into 20mL deionized water, heat to 95°C, stir at 400r / min for 40min, and then add 10g of urea, continue to stir for 30 minutes and then drip into the composite powder at 2mL / min to mix evenly, then transfer to the granulator to granulate, sieve out the particles with a particle size of 1.0mm to obtain spherical pellets, and place the spherical pellets Dry it
PUM
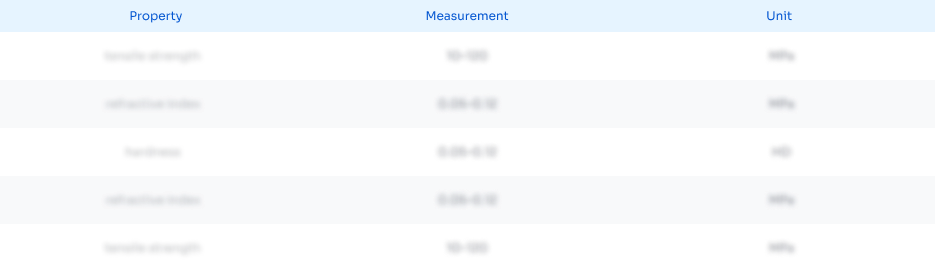
Abstract
Description
Claims
Application Information
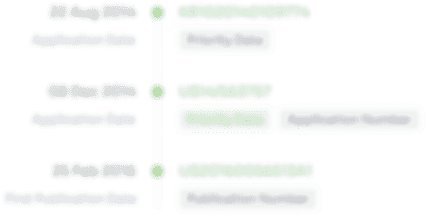
- R&D Engineer
- R&D Manager
- IP Professional
- Industry Leading Data Capabilities
- Powerful AI technology
- Patent DNA Extraction
Browse by: Latest US Patents, China's latest patents, Technical Efficacy Thesaurus, Application Domain, Technology Topic.
© 2024 PatSnap. All rights reserved.Legal|Privacy policy|Modern Slavery Act Transparency Statement|Sitemap