Thin film transistor and manufacturing method thereof and display substrate
A technology of thin film transistors and manufacturing methods, applied in the direction of transistors, semiconductor/solid-state device manufacturing, electric solid-state devices, etc., can solve problems such as high production costs, low production efficiency, and the inability of metal oxide materials to replace conductive materials, so as to reduce production cost, productivity improvement effect
- Summary
- Abstract
- Description
- Claims
- Application Information
AI Technical Summary
Benefits of technology
Problems solved by technology
Method used
Image
Examples
Embodiment Construction
[0040] Due to the high mobility of metal oxides, they are more and more widely used in thin film transistors. However, metal oxides cannot replace metal materials due to their electrical conductivity. As a result, the source and drain electrodes of thin film transistors and the active layer need to be manufactured in different film-forming chambers, which reduces the production efficiency of products and increases production costs.
[0041] In order to solve the above technical problems, the present invention provides a method for manufacturing a thin film transistor, comprising:
[0042] Forming a source electrode, a drain electrode and an active layer;
[0043] It is characterized in that the steps of forming the source electrode, the drain electrode and the active layer include:
[0044] Under a first preset oxygen content atmosphere, a first film is formed using a first metal oxide material, and under a second preset oxygen content atmosphere, a second film is formed using a
PUM
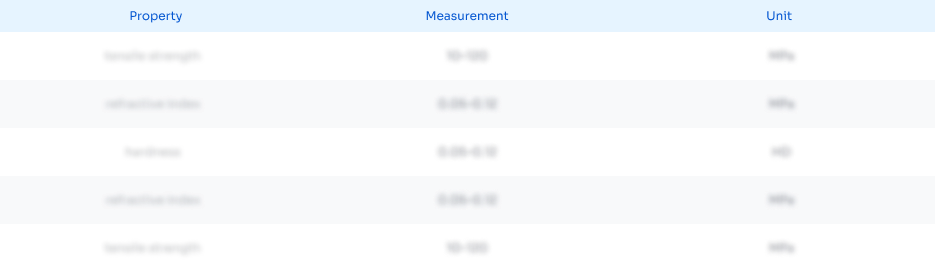
Abstract
Description
Claims
Application Information
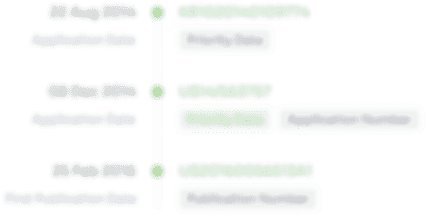
- R&D Engineer
- R&D Manager
- IP Professional
- Industry Leading Data Capabilities
- Powerful AI technology
- Patent DNA Extraction
Browse by: Latest US Patents, China's latest patents, Technical Efficacy Thesaurus, Application Domain, Technology Topic.
© 2024 PatSnap. All rights reserved.Legal|Privacy policy|Modern Slavery Act Transparency Statement|Sitemap