Obstructive explosionproof composite and preparation method thereof
A composite material, barrier and explosion-proof technology, used in electrolytic coatings, electrophoretic plating, coatings, etc., to achieve the effect of improving corrosion resistance, high corrosion resistance and protection performance, and less dosage
- Summary
- Abstract
- Description
- Claims
- Application Information
AI Technical Summary
Problems solved by technology
Method used
Examples
Example Embodiment
[0032] Example 1
[0033] Preparation method of barrier explosion-proof composite material:
[0034] The aluminum alloy sheet with a thickness of 0.02mm is selected, and the surface is treated by an alkaline etching process. The degreasing process uses ethyl acetate as a degreasing solvent, and is soaked at 70 °C for 1min; the alkali treatment is 60 °C for 0.5min, and the light emitting process adopts 20 % nitric acid solution at 20°C for 1.5min. Then, the aluminum alloy sheet is made into mesh aluminum alloy foil by cutting and drawing process, and then the functional coating is applied by spraying. Among them, the primer is coated with water-soluble E-20 epoxy ester by electrodeposition, and the thickness is controlled not to exceed 10 microns. The anti-corrosion conductive functional coating adopts E-03 epoxy resin with molecular weight of 6000-8000 and 703 # Soluble phenolic resin is mixed in a ratio of 7:3 (it can take into account the toughness of macromolecular epoxy re
Example Embodiment
[0035] Example 2
[0036] The aluminum alloy sheet with a thickness of 0.02mm is selected, and its surface is polished to make its surface cleanliness not lower than Sa1 level (so that the surface has no visible grease or dirt, and no loosely attached oxide scale, rust and Paint coating and other attachments can significantly improve the adhesion of the resin on its surface), and the rest of the treatment process is the same as in Example 1.
Example Embodiment
[0037] Example 3
[0038] The aluminum alloy sheet with a thickness of 0.02mm was selected, and the surface was subjected to an alkaline etching process. The degreasing process used acetone as the degreasing solvent, the alkali treatment was 50 °C for 1 min, and the light extraction process was 30 °C for 0.5min. Then, the aluminum alloy sheet is made into mesh aluminum alloy foil by cutting and drawing process, and then the functional coating is applied by spraying. Among them, the primer is coated with water-soluble E-20 epoxy ester by electrodeposition, and the thickness is controlled not to exceed 10 microns; the anti-corrosion conductive functional coating is made of epoxy-urethane acrylate and mixed with 10% carbon nanotubes as the conductive agent. , After heating at 120 ℃ for 2 minutes, it is cured by ultraviolet radiation. When the curing degree of the primer is 50%, the mixed anti-corrosion conductive coating is evenly sprayed on the surface of the primer, and the thickn
PUM
Property | Measurement | Unit |
---|---|---|
Thickness | aaaaa | aaaaa |
Thickness | aaaaa | aaaaa |
Volume resistivity | aaaaa | aaaaa |
Abstract
Description
Claims
Application Information
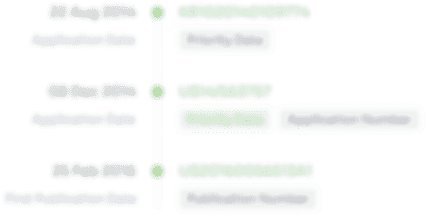
- R&D Engineer
- R&D Manager
- IP Professional
- Industry Leading Data Capabilities
- Powerful AI technology
- Patent DNA Extraction
Browse by: Latest US Patents, China's latest patents, Technical Efficacy Thesaurus, Application Domain, Technology Topic.
© 2024 PatSnap. All rights reserved.Legal|Privacy policy|Modern Slavery Act Transparency Statement|Sitemap