Intelligent forming method for automobile covering part mold
A technology for automotive panels and molding methods, which is applied in vehicle parts, geometric CAD, design optimization/simulation, etc., can solve the problem of low material utilization rate in automotive panel mold manufacturing, achieve improved material utilization rate, reduce skill requirements, The effect of product quality improvement
- Summary
- Abstract
- Description
- Claims
- Application Information
AI Technical Summary
Benefits of technology
Problems solved by technology
Method used
Image
Examples
Embodiment Construction
[0037] The following will clearly and completely describe the technical solutions in the embodiments of the present invention with reference to the accompanying drawings in the embodiments of the present invention. Obviously, the described embodiments are only some, not all, embodiments of the present invention. Based on the embodiments of the present invention, all other embodiments obtained by persons of ordinary skill in the art without making creative efforts belong to the protection scope of the present invention.
[0038] A method for intelligent molding of automobile panel molds, such as figure 1 shown, including the following steps:
[0039] Step 1: Create a standard material sheet;
[0040] Step 2: Compare the part with the standard material sheet;
[0041] Step 3: merging and splitting of parts;
[0042] Step 4: Blanking plan optimization and waste utilization;
[0043] Step 5: Opening drawing and drawing can processing;
[0044] Step 6: Shallow drawing treatment;
PUM
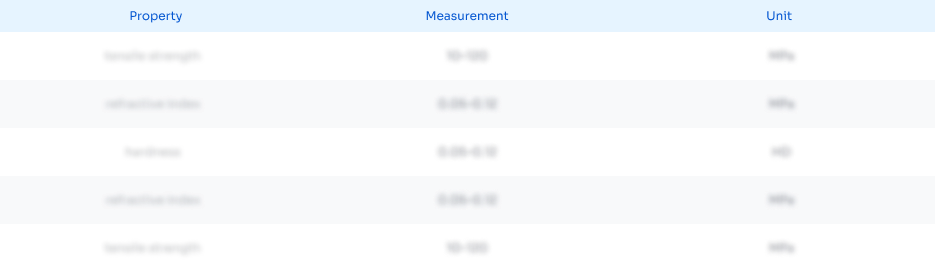
Abstract
Description
Claims
Application Information
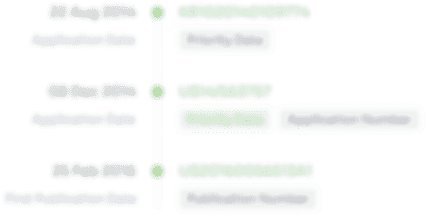
- R&D Engineer
- R&D Manager
- IP Professional
- Industry Leading Data Capabilities
- Powerful AI technology
- Patent DNA Extraction
Browse by: Latest US Patents, China's latest patents, Technical Efficacy Thesaurus, Application Domain, Technology Topic.
© 2024 PatSnap. All rights reserved.Legal|Privacy policy|Modern Slavery Act Transparency Statement|Sitemap