Device and method for testing softness of wire-guide metal hose
A metal hose and testing equipment technology, applied in the direction of applying stable tension/pressure to test material strength, measuring device, strength characteristics, etc., to achieve the effect of reducing test strength, improving test efficiency, and clear physical meaning
- Summary
- Abstract
- Description
- Claims
- Application Information
AI Technical Summary
Problems solved by technology
Method used
Image
Examples
Embodiment Construction
[0028] Describe the present invention below in conjunction with specific embodiment:
[0029] The structural parameters of the wire-conducting metal hose in this embodiment are: outer diameter the inside diameter of Pitch 6.5mm±0.5mm, minimum bending radius ≤60mm.
[0030] figure 1 Shown is the metal hose softness test principle tooling, the metal hose is coiled on the diameter On the disk, the metal hose and the outer surface of the disk are completely in conformity. The metal hose is erected and perpendicular to the ground. A weight with a mass of 0.95kg and a height of 300mm at the lower end is hung on the uppermost end of the metal hose. Remove the disk, and use the height where the weight falls to indicate the softness of the metal hose. When testing the softness of metal hoses, it is required to test a point every 5m. For metal hoses of 50m or longer, the strength of the test directly using the principle tooling is relatively high, the test efficiency is low, and it
PUM
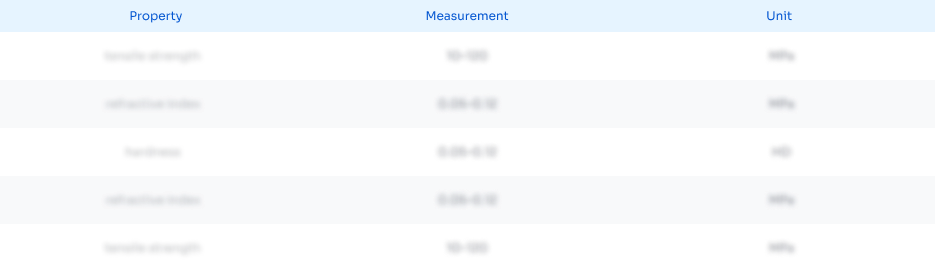
Abstract
Description
Claims
Application Information
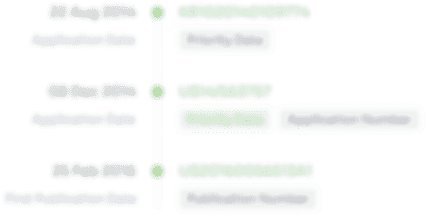
- R&D Engineer
- R&D Manager
- IP Professional
- Industry Leading Data Capabilities
- Powerful AI technology
- Patent DNA Extraction
Browse by: Latest US Patents, China's latest patents, Technical Efficacy Thesaurus, Application Domain, Technology Topic.
© 2024 PatSnap. All rights reserved.Legal|Privacy policy|Modern Slavery Act Transparency Statement|Sitemap