Method for improving durability of GH3536 alloy manufactured by selective laser melting technology
A laser selective melting, GH3536 technology, applied in the direction of improving energy efficiency, additive manufacturing, process efficiency, etc., can solve the problems of large differences in horizontal and vertical structures, uneven high-temperature durability, poor high-temperature durability of alloys, etc. , to achieve the effect of eliminating the inhomogeneity of the alloy structure
- Summary
- Abstract
- Description
- Claims
- Application Information
AI Technical Summary
Problems solved by technology
Method used
Image
Examples
Embodiment 1
[0016] The present embodiment processes the GH3536 alloy manufactured by laser selective melting technology as follows:
[0017] (1) Before heat treatment, clean the powder on the surface and inner cavity of the superalloy parts made by SLM, and blow the surface and inner cavity of the parts with compressed air to ensure that they are cleaned.
[0018] (2) Put the workpiece into a heat treatment furnace (both air furnace and vacuum furnace are acceptable), raise the temperature to 900°C at a rate of 5-10°C / min and keep it for 4 hours, then cool the furnace. The annealing treatment is mainly to eliminate the hidden danger of residual stress during the quenching process of the workpiece prepared by SLM.
[0019] (3) Put the workpiece into the hot isostatic pressing furnace and evacuate to 10 -1 Below Pa, fill with high-purity argon (purity 99.999%), heat up to 1160°C at a heating rate of 5-15°C / min (when the vacuum reaches a certain level, the heating can be turned on to impro
Embodiment 2
[0025] The present embodiment processes the GH3536 alloy manufactured by laser selective melting technology as follows:
[0026] (1) Before heat treatment, clean the powder on the surface and inner cavity of the superalloy parts made by SLM, and blow the surface and inner cavity of the parts with compressed air to ensure that they are cleaned.
[0027] (2) Put the workpiece into a heat treatment furnace (both air furnace and vacuum furnace are acceptable), raise the temperature to 900°C at a rate of 5-10°C / min and keep it for 4 hours, then cool the furnace. The annealing treatment is mainly to eliminate the hidden danger of residual stress during the quenching process of the workpiece prepared by SLM.
[0028] (3) Put the workpiece into the hot isostatic pressing furnace and evacuate to 10 -1 Below Pa, fill with high-purity argon (purity 99.999%), heat up to 1210°C at a heating rate of 5-15°C / min (when the vacuum reaches a certain level, the heating can be turned on to impro
Embodiment 3
[0034] The present embodiment processes the GH3536 alloy manufactured by laser selective melting technology as follows:
[0035] (1) Before heat treatment, clean the powder on the surface and inner cavity of the superalloy parts made by SLM, and blow the surface and inner cavity of the parts with compressed air to ensure that they are cleaned.
[0036] (2) Put the workpiece into a heat treatment furnace (both air furnace and vacuum furnace are acceptable), raise the temperature to 900°C at a rate of 5-10°C / min and keep it for 4 hours, then cool the furnace. The annealing treatment is mainly to eliminate the hidden danger of residual stress during the quenching process of the workpiece prepared by SLM.
[0037] (3) Put the workpiece into the hot isostatic pressing furnace and evacuate to 10 -1 Below Pa, fill with high-purity argon (purity 99.999%), heat up to 1175°C at a heating rate of 5-15°C / min (when the vacuum reaches a certain level, the heating can be turned on to impro
PUM
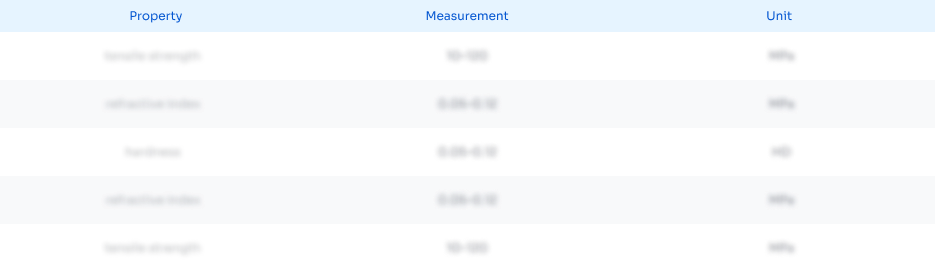
Abstract
Description
Claims
Application Information
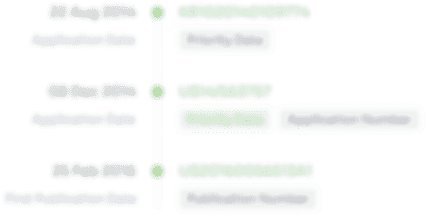
- R&D Engineer
- R&D Manager
- IP Professional
- Industry Leading Data Capabilities
- Powerful AI technology
- Patent DNA Extraction
Browse by: Latest US Patents, China's latest patents, Technical Efficacy Thesaurus, Application Domain, Technology Topic.
© 2024 PatSnap. All rights reserved.Legal|Privacy policy|Modern Slavery Act Transparency Statement|Sitemap