Dyeing and finishing long vehicle finishing method of bio-enzyme treatment
A processing method and bio-enzyme technology, applied in the field of textile printing and dyeing, can solve problems such as limited cloth capacity, unstable color or other quality, and low production efficiency, so as to avoid quality differences, higher production efficiency and fabric quality, and higher production efficiency. high efficiency effect
- Summary
- Abstract
- Description
- Claims
- Application Information
AI Technical Summary
Benefits of technology
Problems solved by technology
Method used
Examples
Embodiment 1
[0026] The specifications of processed fabrics are:
[0027] CM40*SPANDEX30(40D)*217*106*50 / 52, pattern: 4 / 1 satin.
[0028] The dyeing and finishing long car processing method of biological enzyme treatment described in the present embodiment 1 is made up of following operations:
[0029] (1) Padding and fluffing agent for tenter: speed of 50m / min, 2 dips and 2 rollings, temperature of drying room 150°C, padding rate of 70%, padding fluffing agent 9440: 40g / L, drop 139cm.
[0030] (2) Sanding: the vehicle speed is 10m / min, the speed of the sanding roller is 185r / min, the tension is 3bar, and the speed of the large cylinder is 80r / min.
[0031] (3) Stenter padding and polishing enzyme: speed 60m / min, 2 dips and 2 rollings, padding rate 70%, drying room does not heat up, padding and polishing enzyme CR: 4g / L, fan off, fall 139.5 cm, the cloth surface is completely wet, rolled up, and the outsourcing PE film is completely sealed.
[0032] (4) Humid stacking in
Embodiment 2
[0048] The specifications of processed fabrics are:
[0049] CM40*SPANDEX30(40D)*205*90*52 / 53, pattern: 1 / 3Z.
[0050] The dyeing and finishing long car processing method of biological enzyme treatment described in the present embodiment 2 is made up of following operations:
[0051] (1) Padding and fluffing agent for tenter: speed of 50m / min, 2 dips and 2 rollings, drying room temperature: 150°C, padding rate of 70%, padding and fluffing agent 9440: 40g / L, drop 138cm .
[0052] (2) Sanding: the vehicle speed is 20m / min, the speed of the sanding roller is 150r / min, the tension is 3bar, and the speed of the large cylinder is 60r / min.
[0053] (3) Stenter padding and polishing enzyme: speed 50m / min, 2 dips and 2 rollings, padding rate 70%, drying room does not heat up, padding and polishing enzyme CR is in; 4g / L, turn off the fan, and drop 139.5cm, the cloth surface is completely wet, rolled up, and the outsourcing PE film is completely sealed.
[0054] (4) Humi
Embodiment 3
[0070] The specifications of processed fabrics are:
[0071] C / BEM CPT40*LYCRA30(40D)+C / MODAL32 / 2*225*110*53 / 54, pattern: reorganized.
[0072] The dyeing and finishing long car processing method of biological enzyme treatment described in the present embodiment 3 is made up of following operations:
[0073] (1) Padding and fluffing agent for tenter: speed of 50m / min, 2 dips and 2 rollings, drying room temperature of 150°C, padding rate of 70%, padding fluffing agent 9440: 40g / L, drop 138cm.
[0074] (2) Sanding: the vehicle speed is 15m / min, the speed of the sanding roller is 200r / min, the tension is 4bar, and the speed of the large cylinder is 100r / min.
[0075] (3) Stenter padding and polishing enzyme: speed 60m / min, 2 dips and 2 rollings, the padding rate is 70%, the drying room does not heat up, the padding and polishing enzyme CR: 8g / L, the fan is turned off, and the drop is 140cm , the cloth surface is completely wet, rolled up, and the outsourcing
PUM
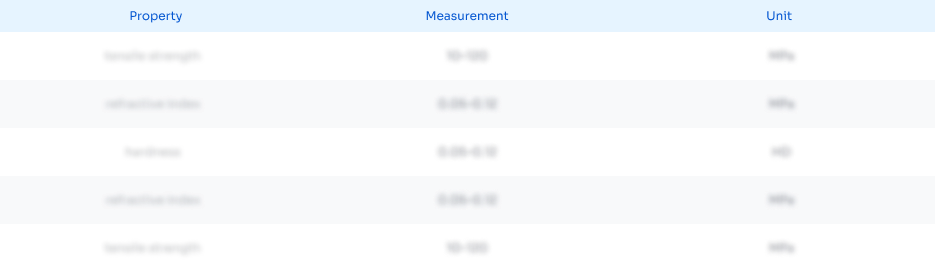
Abstract
Description
Claims
Application Information
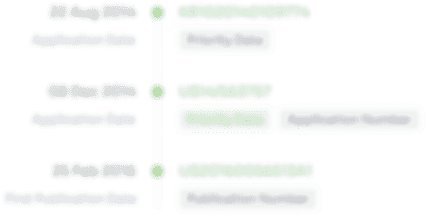
- R&D Engineer
- R&D Manager
- IP Professional
- Industry Leading Data Capabilities
- Powerful AI technology
- Patent DNA Extraction
Browse by: Latest US Patents, China's latest patents, Technical Efficacy Thesaurus, Application Domain, Technology Topic.
© 2024 PatSnap. All rights reserved.Legal|Privacy policy|Modern Slavery Act Transparency Statement|Sitemap