Sleeve grouting material for steel bar connection of prefabricated building
A sleeve grouting and prefabricated technology, applied in sustainable waste treatment, solid waste management, climate sustainability, etc., can solve problems such as hidden quality problems of finished grouting materials, and achieve enhanced activation effect, improved mechanical strength, and improved The effect of fluidity
- Summary
- Abstract
- Description
- Claims
- Application Information
AI Technical Summary
Benefits of technology
Problems solved by technology
Method used
Image
Examples
Embodiment 1
[0041] The sleeve grouting material provided in this embodiment includes the following components by weight: 820 parts of cement, 120 parts of waste concrete active micropowder, 950 parts of quartz sand, 60 parts of composite fiber, and 70 parts of admixture; wherein the waste concrete The active micro powder accounts for about 6% of the total amount of sleeve grout components.
Embodiment 2
[0043] The sleeve grouting material provided in this embodiment includes the following components by weight: 820 parts of cement, 100 parts of waste concrete active micropowder, 950 parts of quartz sand, 60 parts of composite fiber, and 70 parts of admixture; that is, the waste concrete The active micropowder accounts for 5% of the total amount of sleeve grout components.
Embodiment 3
[0045] The sleeve grout provided in this embodiment includes the following components by weight: 820 parts of cement, 143 parts of waste concrete active micropowder, 950 parts of quartz sand, 60 parts of composite fiber, and 70 parts of admixture; that is, the waste concrete The active micro powder accounts for about 7% of the total amount of sleeve grout components.
PUM
Property | Measurement | Unit |
---|---|---|
Particle size | aaaaa | aaaaa |
Particle size | aaaaa | aaaaa |
Particle size | aaaaa | aaaaa |
Abstract
Description
Claims
Application Information
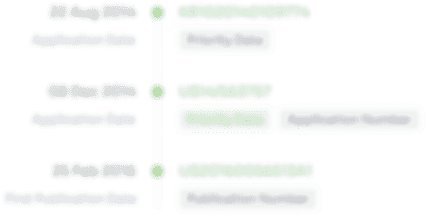
- R&D Engineer
- R&D Manager
- IP Professional
- Industry Leading Data Capabilities
- Powerful AI technology
- Patent DNA Extraction
Browse by: Latest US Patents, China's latest patents, Technical Efficacy Thesaurus, Application Domain, Technology Topic.
© 2024 PatSnap. All rights reserved.Legal|Privacy policy|Modern Slavery Act Transparency Statement|Sitemap