Scratch-resistant polypropylene material and preparation method thereof
A polypropylene material and scratch-resistant technology, applied in the field of scratch-resistant polypropylene materials and their preparation, can solve problems such as blooming, reducing product aesthetics, whitening, etc., to reduce scratches and improve scratch resistance. Effect
- Summary
- Abstract
- Description
- Claims
- Application Information
AI Technical Summary
Benefits of technology
Problems solved by technology
Method used
Image
Examples
preparation example 1
[0036] Preparation of modified chitosan fiber: Weigh 3 parts of silver nitrate and dissolve it in 100 parts of deionized water, and stir evenly; weigh 15 parts of cut chitosan fiber and add it to the above silver nitrate solution, and keep stirring; Dissolve 1 part of sodium borohydride in 100 parts of deionized water to obtain a sodium borohydride solution, weigh 3 parts of the above-mentioned sodium borohydride solution and add it to the above-mentioned silver nitrate solution, and keep stirring. After 2 minutes of reaction, the chitosan fiber Take it out, wash it several times with distilled water, and then dry it to obtain the modified chitosan fiber.
preparation example 2
[0038]Preparation of ore filler: Weigh 15 parts of sodium carbonate and dissolve in 100 parts of deionized water, then weigh 10 parts of diatomaceous earth and 10 parts of quartz and add to the sodium carbonate solution, weigh 20 parts of zinc nitrate and add to the above solution 20 minutes later, the obtained diatomite and quartz particles were washed and dried, and then baked at 500°C for 3 hours, and the diatomite, quartz and calcium carbonate were mixed in a weight ratio of 3:3 : 2 for mixing to obtain ore filler. Before use, diatomaceous earth, quartz and calcium carbonate are all ball-milled and passed through a 1200-mesh sieve before use.
Embodiment 1
[0041] Weigh 60 parts of polypropylene, 20 parts of modified chitosan fiber, 10 parts of ore filler, 1 part of silane coupling agent, 0.5 part of lubricant, 3 parts of compatibilizer and 0.5 part of antioxidant, and mix uniformly; The mixture is added to the screw extruder for melt extrusion, the temperature of the front section of the screw extruder is controlled to be 190°C, the temperature of the middle section is 185°C, the temperature of the back section is 170°C, and the length-to-diameter ratio of the screw is 45:1. After extrusion, the strands are cooled by cooling water, and then sheared and pelletized to obtain a scratch-resistant polypropylene material.
[0042] Among them, the lubricant is ethylene bis stearamide, the compatibilizer is a mixture of PP-g-MAH and POE-g-MAH with a weight ratio of 1:1, and the antioxidant is phytic acid with a weight ratio of 1:1 and luteolin mixture.
[0043] Embodiment 2-Example 6 On the basis of the method in Example 1, the quality of
PUM
Property | Measurement | Unit |
---|---|---|
Rockwell hardness | aaaaa | aaaaa |
Abstract
Description
Claims
Application Information
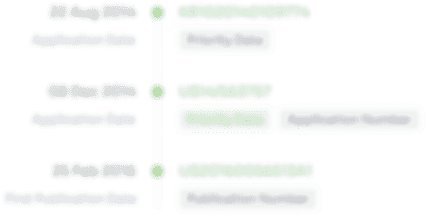
- R&D Engineer
- R&D Manager
- IP Professional
- Industry Leading Data Capabilities
- Powerful AI technology
- Patent DNA Extraction
Browse by: Latest US Patents, China's latest patents, Technical Efficacy Thesaurus, Application Domain, Technology Topic.
© 2024 PatSnap. All rights reserved.Legal|Privacy policy|Modern Slavery Act Transparency Statement|Sitemap