Coating light imitation brick material and processing method of imitation brick
A processing method and imitation brick technology, applied in the field of imitation bricks, can solve the problems of short service life, heavy imitation brick quality, poor water resistance, etc., and achieve the effects of reducing quality, weight and coating weight.
- Summary
- Abstract
- Description
- Claims
- Application Information
AI Technical Summary
Benefits of technology
Problems solved by technology
Method used
Image
Examples
Embodiment 1
[0029] A kind of processing method of imitation brick, comprises the steps:
[0030] Step 1: Prepare as figure 1 A kind of imitation brick processing equipment shown, comprises support plate 1, support frame 2, mold frame 3 and pressing unit; figure 2 As shown, the support frame 2 includes a column 4 and a top plate 5, the upper end of the column 4 and the top plate 5 are fixedly connected by screws; It is fixedly connected with the support block 7 by screws.
[0031] Such as image 3 As shown, the mold frame 3 is provided with a "T"-shaped cavity-forming unit, the cavity-forming unit includes a cavity-forming block 8 and two connecting blocks 9, and the cavity-forming block 8 is connected to the mold frame 3 through the connecting block 9, namely One end of the connection block 9 is fixedly connected with the side wall of the mold frame 3 by screws, and the other end of the connection block 9 is fixedly connected with the cavity forming block 8 by screws, and the width of th
Embodiment 2
[0039] On the basis of Example 1, as figure 1 As shown, the support block 7 is fixedly connected with a support bar 17 by screws, the support bar 17 is arranged obliquely, and the upper end of the support bar 17 is fixedly connected with the column 4 by screws. A rubber pad is bonded to the push-pull rod 15 , and the rubber pad is conducive to increasing the frictional force between the push-pull rod 15 and the hole 14 . The support plate 1 is fixed with a material retaining plate by screws, and the material retaining plate is positioned between the support bar 17 and the mold frame 3 to prevent the imitation brick material from entering the chute 6 .
Embodiment 3
[0041] The difference from Example 1 is that a light-weight imitation brick material for painting includes the following raw materials: 50g of water, 1g of cellulose, 0.5g of MZ bentonite, 0.5g of pH regulator, 3g of wetting and dispersing agent, ethylene glycol 8g, defoamer 0.5g, alcohol ester twelve 3g, preservative 1g, silica sol 5g, styrene-acrylic emulsion 110g, heavy calcium powder 110g, polyvinyl alcohol 0.5g, expanded perlite 20g, titanium dioxide 10g, quartz sand 530g , Thickener 1g.
PUM
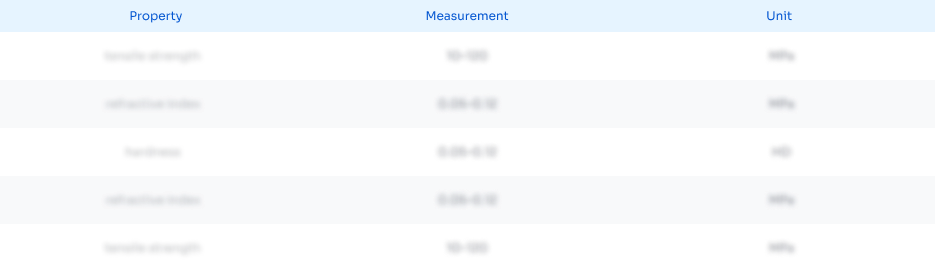
Abstract
Description
Claims
Application Information
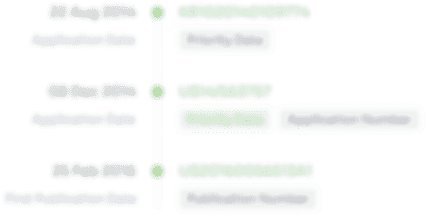
- R&D Engineer
- R&D Manager
- IP Professional
- Industry Leading Data Capabilities
- Powerful AI technology
- Patent DNA Extraction
Browse by: Latest US Patents, China's latest patents, Technical Efficacy Thesaurus, Application Domain, Technology Topic.
© 2024 PatSnap. All rights reserved.Legal|Privacy policy|Modern Slavery Act Transparency Statement|Sitemap