Preparation method and preparation system of solar photovoltaic backboard
A photovoltaic backplane and preparation system technology, applied in the field of solar photovoltaic backplanes, can solve problems such as difficult control of product curing humidity, product peeling force needs to be improved, and product production is not stable enough, so as to achieve a high degree of automation, reduce labor costs, and process simple effect
- Summary
- Abstract
- Description
- Claims
- Application Information
AI Technical Summary
Benefits of technology
Problems solved by technology
Method used
Image
Examples
preparation example Construction
[0047] see figure 1 , a method for preparing a solar photovoltaic backplane, comprising the following steps:
[0048] Step S1: Set the tension parameters of the substrate and the film, and control their continuous running speed to 10-600m / s.
[0049]In a specific embodiment, the unwinding tension of the substrate and the film is controlled to be 10-500N, the tension of the upper bridge is 10-500N, and the tension of the upper bridge is a preset initial tension value or a compensation force value that keeps the tension constant . Described substrate comprises polypropylene film (PP film), polyethylene terephthalate film (PET film), one or more composite films in polyimide film (PI film), wherein composite film It can be a multi-layer film composed of multiple layers of films of different materials, or a single-layer or multi-layer film composed of multiple materials. The covering film includes white polyvinylidene fluoride film (PVDF film), black polyvinylidene fluoride film,
Embodiment 5
[0073] Example 5: On the basis of Example 2, the white PVDF / PET composite film is also obtained by compounding this process, that is, the obtained product structure is white PVDF+solvent-free glue+PET composite film+solvent-free glue+O Film, the The unilateral initial peeling force of the product and the peeling force after PCT48h are all equivalent to Example 2.
PUM
Property | Measurement | Unit |
---|---|---|
Unwind tension | aaaaa | aaaaa |
Winding tension | aaaaa | aaaaa |
Viscosity | aaaaa | aaaaa |
Abstract
Description
Claims
Application Information
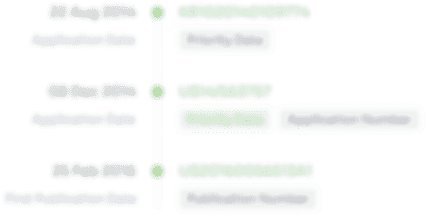
- R&D Engineer
- R&D Manager
- IP Professional
- Industry Leading Data Capabilities
- Powerful AI technology
- Patent DNA Extraction
Browse by: Latest US Patents, China's latest patents, Technical Efficacy Thesaurus, Application Domain, Technology Topic.
© 2024 PatSnap. All rights reserved.Legal|Privacy policy|Modern Slavery Act Transparency Statement|Sitemap