Preparation method of glass substrate
A glass substrate, drying treatment technology, applied in the direction of circuit substrate materials, printed circuit manufacturing, reinforcement of conductive patterns, etc., to achieve good application prospects, easy operation, and improved heat dissipation effect
- Summary
- Abstract
- Description
- Claims
- Application Information
AI Technical Summary
Problems solved by technology
Method used
Image
Examples
Example Embodiment
[0019] A method for making a glass substrate, a first aspect of the embodiment of the present application, the process comprising the steps of:
[0020] S01: providing an initial glass substrate;
[0021] S02: Preparation of the conductive pattern on a surface of the starting glass substrate;
[0022] S03: In the back side aluminum paste formed initially coated glass substrate having a conductive pattern, is dried, and then co-sintered to obtain a glass substrate.
[0023] The method of preparing a glass substrate according to an embodiment of the present application, a method for producing a glass substrate circuit board, the production method of the thermal conductivity of the glass substrate obtained is significantly improved, can solve the problem of heat dissipation of the glass substrate; in particular, the initial glass substrate having two opposing surfaces, the aluminum paste prepared in Example a conductive pattern of the surface of the starting substrate, i.e., the other s
Example Embodiment
[0036] Example 1
[0037] A method of preparing a glass substrate copper circuit board, comprising the steps of:
[0038] 1, taken respectively, said copper powder 81g 0.3-0.5μm, the glass frit 9g, diethylene glycol monobutyl ether 6g, dodecanol fat 2g, ethyl cellulose 0.5g, dispersants 0.9g, 0.6g thixotropic agent added to the vessel, the pre-mixed with stirring, and then dispersed with a three roll mill to obtain a fineness blade <5μm of electroconductive copper paste;
[0039] 2, the aluminum powder were weighed 71.25g 2μm ~ 1, and 3.75 g of glass frit, diethylene glycol monobutyl ether 16g, dodecanol fat 4.3g, 3.75 g of ethyl cellulose, a dispersant 0.75g, thixotropic agents 0.2g added to the vessel, stirred pre-mix, and then using a three roll mill dispersion, to give the blade a fineness <5μm of high thermal conductivity aluminum paste;
[0040] 3, the above prepared electroconductive copper paste by screen printing on the corresponding pattern of 2mm ordinary glass, printed wi
Example Embodiment
[0045] Example 2
[0046] A method of preparing a glass substrate copper circuit board, comprising the steps of:
[0047] 1, taken respectively, said copper powder 81g 0.3-0.5μm, the glass frit 9g, diethylene glycol monobutyl ether 6g, dodecanol fat 2g, ethyl cellulose 0.5g, dispersants 0.9g, 0.6g thixotropic agent added to the vessel, the pre-mixed with stirring, and then dispersed with a three roll mill to obtain a fineness blade <5μm of electroconductive copper paste;
[0048] 2, the aluminum powder were weighed 80.75g 2μm ~ 1, and 4.25 g of glass frit, diethylene glycol monobutyl ether 8g, dodecanol 4.65 g of fat, ethyl cellulose 1.2g, 0.85 g dispersant, a thixotropic agent 0.3g added to the vessel, stirred pre-mix, and then using a three roll mill dispersion, to give the blade a fineness <5μm of high thermal conductivity aluminum paste;
[0049] 3, the above prepared electroconductive copper paste by screen printing on the corresponding pattern of 2mm ordinary glass, printed wit
PUM
Property | Measurement | Unit |
---|---|---|
Thickness | aaaaa | aaaaa |
Softening point | aaaaa | aaaaa |
Thickness | aaaaa | aaaaa |
Abstract
Description
Claims
Application Information
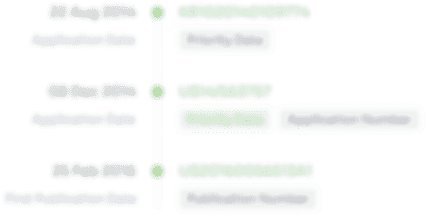
- R&D Engineer
- R&D Manager
- IP Professional
- Industry Leading Data Capabilities
- Powerful AI technology
- Patent DNA Extraction
Browse by: Latest US Patents, China's latest patents, Technical Efficacy Thesaurus, Application Domain, Technology Topic.
© 2024 PatSnap. All rights reserved.Legal|Privacy policy|Modern Slavery Act Transparency Statement|Sitemap