Glaze material and preparation method thereof
A glaze and raw material technology, applied in the field of glaze and its preparation, can solve the problems of wasting production time, prone to agglomeration, increase production cost, etc., and achieve the effects of improving effect, improving dispersion effect, and improving heat dissipation capacity.
- Summary
- Abstract
- Description
- Claims
- Application Information
AI Technical Summary
Problems solved by technology
Method used
Examples
Example Embodiment
[0020] The invention provides a method for preparing a glaze, which includes the following steps:
[0021] (1) Weigh the dry raw materials in the glaze formula according to the formula amount, and add them to the mixing tank of the planetary mixer to stir and mix to obtain a dry raw material mixture;
[0022] (2) Transfer the dry raw material mixture to a ball mill, add 5-10% of the total weight of water to wet the dry raw material mixture, ball mill, and pass through 800-1200 mesh sieve after ball milling;
[0023] (3) Transfer the sieved dry raw material mixture to the mixing tank of the planetary mixer, add the remaining amount of water, vacuum to -0.05~-0.1MPa, vacuum stir and mix for 50~60min, and finally adjust the moisture content to 53-58% to obtain the glaze.
[0024] In the present invention, the dry materials in the glaze formula are pre-mixed, so that the dry materials are mixed more fully and uniformly, which avoids that the dry materials and water in the prior art are prone
Example Embodiment
[0053] Example 1
[0054] A method for processing ceramic products includes the following steps:
[0055] S1: Blank processing and blank forming processing,
[0056] Including pulverizing and sieving the massive solid materials to obtain granular raw materials; then successively removing iron, mud dewatering, aging, sludge scouring, and granulation to obtain billets with particle gradation and good fluidity;
[0057] The blank is formed into the shape of a ceramic product, and then the surface of the blank is sprayed at high speed with mixed abrasive, and then dried to obtain a green body;
[0058] The mixed abrasive includes a mixture of aluminum oxide, silicon oxide, diamond powder and glass powder. Each raw material component is ball milled and passed through a 1100 mesh sieve, and the mass ratio of aluminum oxide, silicon oxide, diamond powder and glass powder is 1 : 0.3: 1.4: 0.6;
[0059] The conditions of the high-speed spraying include: using nitrogen as a carrier gas, the output o
Example Embodiment
[0067] Example 2
[0068] The method for processing ceramic products is as provided in Example 1, except that in step S2, the glaze includes the following raw materials by weight: 28 parts of potash feldspar, 35 parts of quartz, 10 parts of talc, and 5 parts of corundum , 5 parts of glass powder, 3 parts of alumina powder, 4 parts of sodium silicate, 1 part of diamond powder, 10 parts of cobalt green pigment, 70 parts of water;
[0069] Otherwise, the ceramic products were processed according to the processing method of Example 1.
PUM
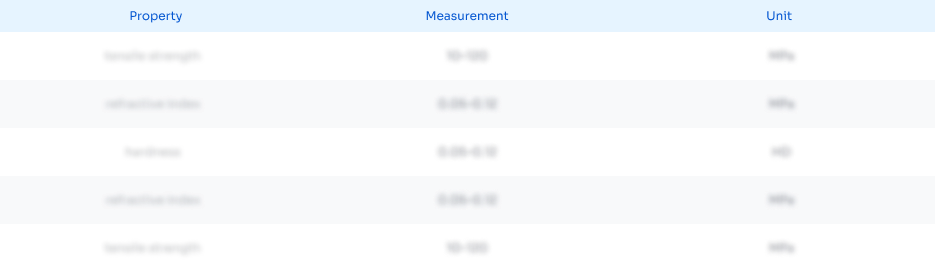
Abstract
Description
Claims
Application Information
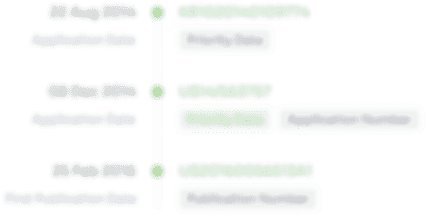
- R&D Engineer
- R&D Manager
- IP Professional
- Industry Leading Data Capabilities
- Powerful AI technology
- Patent DNA Extraction
Browse by: Latest US Patents, China's latest patents, Technical Efficacy Thesaurus, Application Domain, Technology Topic.
© 2024 PatSnap. All rights reserved.Legal|Privacy policy|Modern Slavery Act Transparency Statement|Sitemap