Nano-level ultra-high heat-conducting titanium-carbon composite material and preparation method thereof
A technology of composite materials and manufacturing methods, applied in the field of nano-scale ultra-high thermal conductivity titanium-carbon composite materials and its manufacturing, can solve the problems of hard-to-get, expensive diamonds, etc., and achieve enhanced physical structure strength, low production cost, and simple process Effect
- Summary
- Abstract
- Description
- Claims
- Application Information
AI Technical Summary
Benefits of technology
Problems solved by technology
Method used
Examples
Embodiment 1
[0014] Weigh 60Kg of acidified expanded graphite with a carbon content of 90%, 20Kg of flake graphite nano-powder with a carbon content of 90%, 10Kg of titanium metal nano-powder and 10Kg of mesophase nano-carbon powder, and gradually put them into a high-temperature reaction furnace. Under the protection of gas, the temperature is gradually raised and mixed for 3 hours at a temperature of 350°C-500°C to obtain a thick high-temperature mixed carbon-making mixed liquid, and then the thick high-temperature mixed carbon-making mixed liquid is hot-molded, and the molding temperature is 450 °C, The pressure was 300 MPa and it was molded into sheets, and finally the molded material was carbonized at 1000°C for 1 hour, and then graphitized at 3000°C for 1 hour. The resulting material has a thermal conductivity of 517 W / mK and a density of 1.81 g / cm 3 .
Embodiment 2
[0016] Weigh 65Kg of acidified expanded graphite with a carbon content of 92%, 10Kg of flake graphite nanopowder with a carbon content of 91%, 15Kg of titanium metal nanopowder and 10Kg of mesophase nanometer carbon powder, and gradually put them into a high-temperature reaction furnace under the protection of inert gas. The temperature is gradually raised and mixed for 2 hours at a temperature of 300°C-500°C to obtain a thick high-temperature mixed carbon-making mixed liquid. Then, the dense carbon mixed liquid was rolled at a temperature of 400°C and a pressure of 180MPa to form a sheet. Finally, the rolled material was carbonized at 900°C for 4 hours and graphitized at 2500°C for 4 hours. The resulting material has a thermal conductivity of 563 W / mK and a density of 1.89 g / cm 3 .
Embodiment 3
[0018] Weigh 70Kg of acidified expanded graphite with a carbon content of 90%, 15Kg of flake graphite nano-powder with a carbon content of 90%, 7Kg of titanium metal nano-powder and 8Kg of mesophase nano-carbon powder, and gradually put them into a high-temperature reaction furnace under the protection of inert gas, Gradually heat up and mix for 3 hours at a temperature of 350°C-450°C to obtain a thick high-temperature mixed carbon-making mixed liquid, and then hot-molding the thick high-temperature mixing carbon-making mixed liquid, the molding temperature is 325 °C, and the pressure is 230MPa. Formed into sheets, the molded material was finally carbonized at 920°C for 6 hours and graphitized at 2900°C for 6 hours. The resulting material has a thermal conductivity of 610 W / mK and a density of 1.93 g / cm 3 .
PUM
Property | Measurement | Unit |
---|---|---|
Thermal conductivity | aaaaa | aaaaa |
Density | aaaaa | aaaaa |
Thermal conductivity | aaaaa | aaaaa |
Abstract
Description
Claims
Application Information
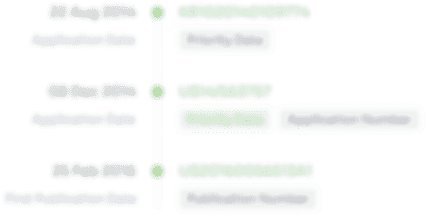
- R&D Engineer
- R&D Manager
- IP Professional
- Industry Leading Data Capabilities
- Powerful AI technology
- Patent DNA Extraction
Browse by: Latest US Patents, China's latest patents, Technical Efficacy Thesaurus, Application Domain, Technology Topic.
© 2024 PatSnap. All rights reserved.Legal|Privacy policy|Modern Slavery Act Transparency Statement|Sitemap