Injection moulding process of polyethylene (PE) material pieces for infusion apparatus
An infusion set and process technology, applied in the coating and other directions, can solve the problems of raw material waste, short shot, shrinkage cavities, etc., and achieve the effect of improving the degree of automation, shortening the cycle time, and saving raw materials
- Summary
- Abstract
- Description
- Claims
- Application Information
AI Technical Summary
Benefits of technology
Problems solved by technology
Method used
Examples
Embodiment 1
[0016] Injection molding process of PE material parts for infusion sets, which includes the following steps:
[0017] S1, sol, the barrel of the injection molding machine is sequentially divided into four sections of the barrel, three sections of the barrel, two sections of the barrel, and one section of the barrel along the direction from the feed port to the nozzle, and the temperature of the barrel nozzle of the injection molding machine is heated to 210°C, heat the first section of the barrel to 215°C, heat the second section of the barrel to 215°C, heat the third section of the barrel to 210°C, and heat the fourth section of the barrel to 200°C; PE added to the barrel The plastic is heated to a molten state by the barrel;
[0018] S2, mold closing, the mold closing time is 3s;
[0019] S3. Injecting glue, injecting molten PE plastic into the mold through the nozzle, the injection speed is 90% of the maximum speed, and the injection pressure is 110bar; the maximum speed refe
Embodiment 2
[0025] Injection molding process of PE material parts for infusion sets, which includes the following steps:
[0026] S1, sol, the barrel of the injection molding machine is sequentially divided into four sections of the barrel, three sections of the barrel, two sections of the barrel, and one section of the barrel along the direction from the feed port to the nozzle, and the temperature of the barrel nozzle of the injection molding machine is heated to 220°C, heat the first section of the barrel to 225°C, heat the second section of the barrel to 225°C, heat the third section of the barrel to 225°C, and heat the fourth section of the barrel to 210°C; PE added to the barrel The plastic is heated to a molten state by the barrel;
[0027] S2, mold closing, the mold closing time is 2s;
[0028] S3. Injecting glue, injecting molten PE plastic into the mold through the nozzle, the injection speed is 80% of the maximum speed, and the injection pressure is 100bar; the maximum speed refe
Embodiment 3
[0034] Injection molding process of PE material parts for infusion sets, which includes the following steps:
[0035] S1, sol, the barrel of the injection molding machine is sequentially divided into four sections of the barrel, three sections of the barrel, two sections of the barrel, and one section of the barrel along the direction from the feed port to the nozzle, and the temperature of the barrel nozzle of the injection molding machine is heated to 230°C, heat the first section of the barrel to 235°C, heat the second section of the barrel to 235°C, heat the third section of the barrel to 230°C, and heat the fourth section of the barrel to 220°C; PE added to the barrel The plastic is heated to a molten state by the barrel;
[0036] S2, mold closing, the mold closing time is 1s;
[0037] S3, glue injection, inject the PE plastic in molten state into the mold through the nozzle, the injection speed is 70% of the maximum speed, and the injection pressure is 90bar; the maximum s
PUM
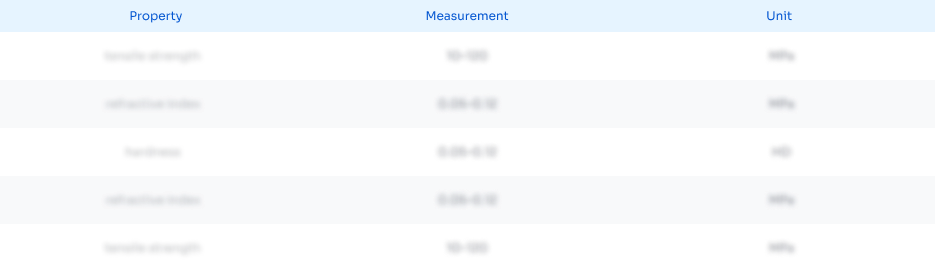
Abstract
Description
Claims
Application Information
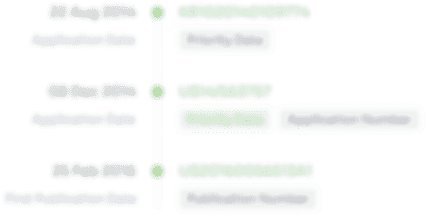
- R&D Engineer
- R&D Manager
- IP Professional
- Industry Leading Data Capabilities
- Powerful AI technology
- Patent DNA Extraction
Browse by: Latest US Patents, China's latest patents, Technical Efficacy Thesaurus, Application Domain, Technology Topic.
© 2024 PatSnap. All rights reserved.Legal|Privacy policy|Modern Slavery Act Transparency Statement|Sitemap