Method for eliminating resin film and method for producing laminate
A manufacturing method, resin film technology, applied in the direction of chemical instruments and methods, lamination, layered products, etc., can solve the problems of unoptimized, optical defects, etc., and achieve the effect of efficient removal
- Summary
- Abstract
- Description
- Claims
- Application Information
AI Technical Summary
Problems solved by technology
Method used
Image
Examples
Embodiment 1
[0112] (Production of reinforcing plate)
[0113] The glass plate of the reinforcing plate uses a glass plate (manufactured by Asahi Glass Co., Ltd., AN100, alkali-free glass) of length 720 mm × width 600 mm × thickness 0.4 mm obtained by the float method. The average linear expansion coefficient of the glass plate is 38×10 -7 / ℃.
[0114] The glass plate was cleaned with pure water and UV cleaned to clean the surface of the glass plate. Then, 100 parts by mass of solvent-free addition reaction type silicone (manufactured by Shinetsu Silicone Co., Ltd., KNS-320A) and 5 parts by mass of platinum-based catalyst (Shinetsu Silicone Co.) were coated on the surface of the glass plate with a spin coater. ,Ltd., CAT-PL-56) mixture (coating amount 20g / m 2 ).
[0115] The solvent-free addition reaction type silicone includes a linear organoalkenyl polysiloxane (main agent) having a vinyl group and a methyl group bonded to a silicon atom, and a hydrogen atom and a methyl group bonded to the
Embodiment 2
[0130] In Example 2, a linear polyorganosiloxane having vinyl groups at both ends (manufactured by Arakawa Chemical Industry Co., Ltd., 8500) and a methylhydrogenpolysiloxane having a hydrosilyl group in the molecule ( The mixture of Arakawa Chemical Industry Co., Ltd. 12031) and a platinum-based catalyst (Arakawa Chemical Industry Co., Ltd., CAT12070) was used as a curable resin composition for forming the resin layer. Reinforcing was prepared in the same manner as in Example 1, except that board.
[0131] Here, the mixing ratio of the linear polyorganosiloxane and the methylhydrogenpolysiloxane is adjusted so that the molar ratio of the vinyl group and the hydrosilyl group is 1:1. In addition, the amount of the platinum-based catalyst was 5 parts by mass relative to 100 parts by mass in total of the linear polyorganosiloxane and methylhydrogenpolysiloxane.
[0132] Then, in the same manner as in Example 1, the figure 2 After heat-processing the laminated body shown, the peeling op
Embodiment 3
[0137] In Example 3, the same as in Example 2 was produced as figure 2 After heat-processing the laminated body shown, the peeling operation of the glass substrate and the reinforcing plate is performed.
[0138] After the peeling operation, by heating the reinforcing plate in the atmosphere at 370°C for 5 minutes, the surface of the resin layer (resin film) opposite to the glass plate was exposed to the atmosphere at 370°C for 5 minutes. After that, the reinforcing plate was cooled from 370°C to 50°C at an average cooling rate of 15°C / sec, and then cooled to room temperature. Next, brush cleaning with isoparaffin solution (manufactured by Idemitsu Kosan Co., Ltd., IP SOLVENT 2028, solubility parameter of 7, flash point of 86°C) for 1 minute, and after washing off the resin layer (resin film), heating by blowing Air to 200°C to remove the solvent.
[0139] The isoparaffin solution described above contains 80.5% by mass of isohexadecane, 3.0% by mass of isotridecane, and 16.5% by m
PUM
Property | Measurement | Unit |
---|---|---|
Average linear expansion coefficient | aaaaa | aaaaa |
Abstract
Description
Claims
Application Information
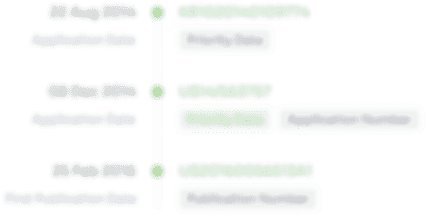
- R&D Engineer
- R&D Manager
- IP Professional
- Industry Leading Data Capabilities
- Powerful AI technology
- Patent DNA Extraction
Browse by: Latest US Patents, China's latest patents, Technical Efficacy Thesaurus, Application Domain, Technology Topic.
© 2024 PatSnap. All rights reserved.Legal|Privacy policy|Modern Slavery Act Transparency Statement|Sitemap