Deformed reinforced bar for American standard concrete and production method thereof
A technology of deformed steel bar and production method, applied in the field of deformed steel bar for American standard concrete and its production, can solve the problems of compressing the profit space of production enterprises, high alloying cost, reducing production enthusiasm of enterprises, etc., so as to enhance market competitiveness and reduce Production cost, beneficial effect of protection
- Summary
- Abstract
- Description
- Claims
- Application Information
AI Technical Summary
Problems solved by technology
Method used
Examples
Example Embodiment
[0031] Example 1
[0032] The production of deformed steel bars for American standard concrete of the present invention includes the following steps of converter smelting, ladle argon blowing, continuous casting, and rolling. among them:
[0033] In the converter smelting process, high-carbon ferromanganese and ferrosilicon alloy are used to deoxidize and alloy molten steel without adding ferrochrome. The smelting process uses high-stretch supplementary blowing, and the control end point [C] is 0.23wt%, and barium alloy The amount of barium alloy added is 1.15kg / t steel, and it is uniformly added to the steel flow during the steel release process; and the chemical composition of the molten steel in this process is controlled: C: 0.40wt%, Si: 0.29wt%, Mn: 1.38 wt%, Cr: 0wt%, P: 0.025wt%, S: 0.024wt%, the rest is Fe and unavoidable impurities;
[0034] In the ladle argon blowing process: After the component temperature is appropriate, perform the "soft blowing" operation, the soft blo
Example Embodiment
[0037] Example 2
[0038] The production of deformed steel bars for American standard concrete of the present invention includes the following steps of converter smelting, ladle argon blowing, continuous casting, and rolling. among them:
[0039] In the converter smelting process: high-carbon ferromanganese, ferrosilicon alloy and ferrochrome are used for alloying. Among them, ferrochrome is added to the impact zone of the ladle steel flow with the steel flow at the later stage of the addition of high-carbon ferromanganese and ferrosilicon alloy. The smelting process adopts high Stretch blow, control the end point [C] is 0.25wt%, use barium alloy to deoxidize, the amount of barium alloy is 1.05kg / t steel, in the process of discharging steel, add it evenly to the steel flow; and control the molten steel in this process The chemical composition is: C: 0.39wt%, Si: 0.28wt%, Mn: 1.40wt%, Cr: 0.36wt%, P: 0.021wt%, S: 0.026wt%, the rest is Fe and unavoidable impurities;
[0040] In the la
Example Embodiment
[0043] Example 3
[0044] The production of deformed steel bars for American standard concrete of the present invention includes the following steps of converter smelting, ladle argon blowing, continuous casting, and rolling. among them:
[0045] In the converter smelting process: high-carbon ferromanganese, ferrosilicon alloy and ferrochrome are used for alloying. Among them, ferrochrome is added to the impact zone of the ladle steel flow with the steel flow at the later stage of the addition of high-carbon ferromanganese and ferrosilicon alloy. The smelting process adopts high Stretch blowing, the control end point [C] is 0.29wt%, the barium alloy is used for deoxidation, the barium alloy is added at 0.9kg / t steel, and the steel is added evenly in the process of releasing the steel; and the molten steel in this process is controlled The chemical composition is: C: 0.42wt%, Si: 0.32wt%, Mn: 1.44wt%, Cr: 0.42wt%, P: 0.017wt%, S: 0.023wt%, the rest is Fe and unavoidable impurities.
PUM
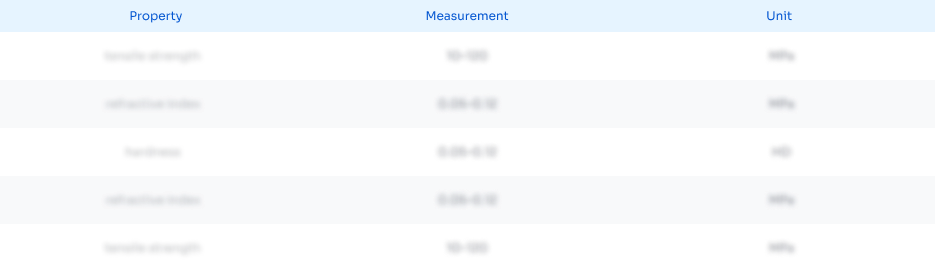
Abstract
Description
Claims
Application Information
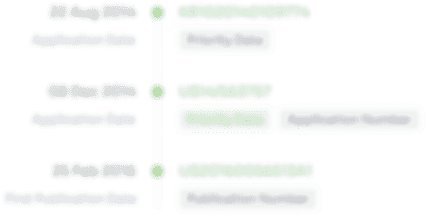
- R&D Engineer
- R&D Manager
- IP Professional
- Industry Leading Data Capabilities
- Powerful AI technology
- Patent DNA Extraction
Browse by: Latest US Patents, China's latest patents, Technical Efficacy Thesaurus, Application Domain, Technology Topic.
© 2024 PatSnap. All rights reserved.Legal|Privacy policy|Modern Slavery Act Transparency Statement|Sitemap