Preparation technology of perfluoropolyether for resin
A technology for perfluoropolyether and preparation process, applied in the field of perfluoropolyether preparation technology, can solve the problems of difficult to obtain catalyst, long reaction time, low reaction temperature and the like
- Summary
- Abstract
- Description
- Claims
- Application Information
AI Technical Summary
Benefits of technology
Problems solved by technology
Method used
Examples
example 1
[0016] Add 10.7 g of cesium fluoride, 50 ml of 1,3-trifluoromethylbenzene, and 20 ml of tetraglyme into a 2-liter double-layer glass reactor equipped with a stirrer, and stir for 30 minutes. Put a cooling medium in the interlayer of the glass reactor, lower the system temperature to -40°C, add 0.5 kg of oxypropane hexafluoride within 3 hours under full stirring and pressure, and control the system temperature at -40°C~ Between -20°C. After the addition, continue to insulate and stir the reaction for 18 hours. Slowly increase the reaction temperature to 20° C., and continue the reaction for 2 hours. No pressure in the system indicates that the monomer has been completely converted. Heat to 115°C with stirring, stir for 0.5 hours, cool and stand to separate layers, separate the polymer in the lower layer, and distill under reduced pressure to remove the solvent to obtain 0.48 kg of the product. The average molecular weight of the polymer obtained by end group titration was 1900.
example 2
[0018] Add 11.84 g of cesium fluoride, 100 ml of 1,3-trifluoromethylbenzene, and 24 ml of tetraglyme into a 2-liter double-layer glass reactor equipped with a stirrer, and stir for 30 minutes. Pass cooling medium into the interlayer of the glass reactor, lower the system temperature to -40°C, add 1 kg of oxypropane hexafluoride within 3 hours under full stirring and pressure, and control the system temperature at -40°C~ Between -20°C. After the addition, continue to insulate and stir the reaction for 28 hours. Slowly increase the reaction temperature to 20° C., and continue the reaction for 2 hours. No pressure in the system indicates that the monomer has been completely converted. Heat to 115°C with stirring, stir for 0.5 hours, cool and stand to separate layers, separate the polymer in the lower layer, and distill under reduced pressure to remove the solvent to obtain 0.97 kg of the product. The average molecular weight of the polymer obtained by end group titration was 2300.
example 3
[0020] Add 15.6 g of cesium fluoride, 80 ml of 1,3-trifluoromethylbenzene, and 30 ml of tetraglyme into a 2-liter double-layer glass reactor equipped with a stirrer, and stir for 30 minutes. Put a cooling medium in the interlayer of the glass reactor, lower the system temperature to -40°C, add 1.5 kg of oxypropane hexafluoride within 5 hours under full stirring and pressure, and control the system temperature at -40°C~ Between -20°C. After adding, continue to insulate and stir the reaction for 25 hours. Slowly increase the reaction temperature to 20° C., and continue the reaction for 2 hours. No pressure in the system indicates that the monomer has been completely converted. Heat to 115°C with stirring, stir for 0.5 hours, cool and stand to separate layers, separate the polymer in the lower layer, and distill under reduced pressure to remove the solvent to obtain 1.45 kg of the product. The average molecular weight of the polymer obtained by end group titration was 2000.
PUM
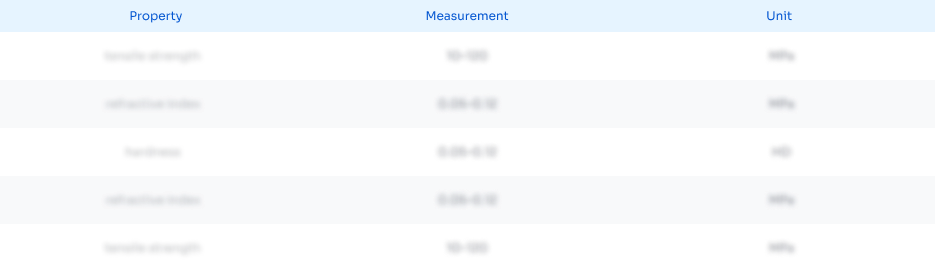
Abstract
Description
Claims
Application Information
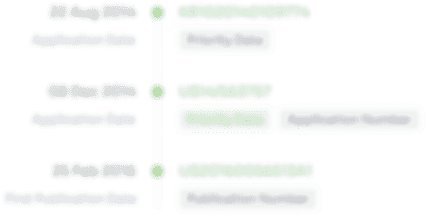
- R&D Engineer
- R&D Manager
- IP Professional
- Industry Leading Data Capabilities
- Powerful AI technology
- Patent DNA Extraction
Browse by: Latest US Patents, China's latest patents, Technical Efficacy Thesaurus, Application Domain, Technology Topic.
© 2024 PatSnap. All rights reserved.Legal|Privacy policy|Modern Slavery Act Transparency Statement|Sitemap