Continuous preparation method of flame retardant polyether polyol
A technology of polyether polyol and flame-retardant polyether, which is applied in the field of continuous preparation of flame-retardant polyether polyol, can solve the problem of insufficient flame-retardant performance of flame-retardant polyether polyol, insufficient oxygen index of polyurethane foam, and short reaction time. Long-term problems, to achieve the effect of good storage stability, good flame retardant performance, shortened production cycle
- Summary
- Abstract
- Description
- Claims
- Application Information
AI Technical Summary
Benefits of technology
Problems solved by technology
Method used
Image
Examples
Embodiment 1
[0047] Embodiment 1: the preparation of dispersant R
[0048] Add 29.8kg of castor oil and 30.0kg of PEG300 into a 200L closed reactor with a dropping device, raise the temperature at 55-60°C, and slowly add 75.0kg of diphenylmethane diisocyanate into the reactor (within 2-2.5h dropwise), remove the heat of reaction in time during the reaction to ensure that the temperature of the reaction system is at 55-60°C, after the dropwise addition, keep warm for 1.0h, and finally add 12.4kg of ethylene glycol dropwise slowly to the reaction system for capping After the reaction, after the dropwise addition, the temperature was kept for 0.5h, and the material was discharged after the reaction to obtain 141.1kg of dispersant R.
Embodiment 2
[0049] Embodiment 2: the preparation of polyether component B
[0050] Add 380kg of polyether polyol Q-1, 3.9kg of dispersant R in Example 1, and 16.2kg of aluminum hydroxide (particle size 100nm) into a stirred reactor to prepare polyether component B-1;
[0051] Add 380kg of Q-1 polyether polyol, 3.9kg of dispersant R in Example 1, 8.1kg of microencapsulated red phosphorus (particle size 80nm) and 8.1kg of aluminum hydroxide (particle size 100nm) into the reactor with stirring Thoroughly stir to prepare polyether component B-2;
[0052] Add 350kg of Q-2 polyether polyol, 3.6kg of dispersant R in Example 1 and 15kg of magnesium hydroxide (particle size 100nm) into a stirred reactor and stir well to prepare polyether component B-3;
[0053] Add 350kg of Q-2 polyether polyol, 3.6kg of dispersant R in Example 1, 7.5kg of expanded graphite (particle size 80nm) and 7.5kg of magnesium hydroxide (particle size 100nm) into the stirred reactor and stir well, Preparation of polyether
Embodiment 3
[0056] Embodiment 3: the synthesis of flame-retardant polyether polyol J-1
[0057] see figure 1 , 44 parts of hydroxyl compound A and 56 parts of polyether component B-1 are continuously pumped into preheater 1 and preheater 2 at a flow rate of 6L / min via a delivery pump to preheat to 90~ 93°C, and then input into the reaction tower through high-pressure pump 1 and high-pressure pump 2 for collision reaction. ~70Kpa, after the material reacts in the reaction tower for 23 minutes, the crude grafted flame-retardant polyether polyol is obtained; the crude grafted flame-retardant polyether polyol is quickly transported to the top of the first-stage spray drying tower at a flow rate of 10L / min Spray feed inlet, the vacuum in the first-level spray drying tower is 13-15Kpa, the temperature is 150-153°C, after the thick grafted flame-retardant polyether polyol stays in the first-level spray drying tower for 17min, Then transport the material to the secondary spray drying tower a
PUM
Property | Measurement | Unit |
---|---|---|
Particle size | aaaaa | aaaaa |
Particle size | aaaaa | aaaaa |
Hydroxyl value | aaaaa | aaaaa |
Abstract
Description
Claims
Application Information
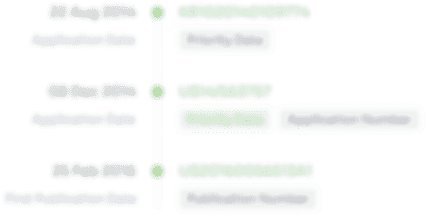
- R&D Engineer
- R&D Manager
- IP Professional
- Industry Leading Data Capabilities
- Powerful AI technology
- Patent DNA Extraction
Browse by: Latest US Patents, China's latest patents, Technical Efficacy Thesaurus, Application Domain, Technology Topic.
© 2024 PatSnap. All rights reserved.Legal|Privacy policy|Modern Slavery Act Transparency Statement|Sitemap