Automotive transmission gear forging method
A technology for automotive transmissions and gears, applied in the field of gear forging, can solve the problems of low safety factor, low investment, and low effective utilization rate of production materials, and achieve the effects of smooth surface quality, improved service life, and superior mechanical properties
- Summary
- Abstract
- Description
- Claims
- Application Information
AI Technical Summary
Benefits of technology
Problems solved by technology
Method used
Examples
Embodiment 1
[0026] A method for forging an automobile transmission gear, comprising the following steps,
[0027] Step 1, blanking, wherein low-carbon steel is selected for heating through a high-frequency electric furnace, and the heating temperature is 1100°C-1300°C;
[0028] Step 2. Process the green body through the cold pressing mold, and use the standard tooth mold to correct the forming teeth;
[0029] Step 3, carburizing, quenching, comprises the following steps,
[0030] Step 1) The blank is preheated, the preheating temperature is controlled at 330°C-380°C, firstly, the blank is degreased to remove surface impurities, secondly, the blank is pre-oxidized to ensure a uniform carburized layer, and finally the blank is It can slow down the heating speed, reduce the unevenness of heating temperature and stress at different positions of different blanks, and reduce the deformation of heat treatment;
[0031] Step 2) Heating and heat preservation, the continuous heating temperature is c
Embodiment 2
[0042] A method for forging an automobile transmission gear, comprising the following steps,
[0043] Step 1, blanking, wherein low-carbon steel is selected for heating through a high-frequency electric furnace, and the heating temperature is 1100°C-1300°C;
[0044] Step 2. Process the green body through the cold pressing mold, and use the standard tooth mold to correct the forming teeth;
[0045] Step 3, carburizing, quenching, comprises the following steps,
[0046] Step 1) The blank is preheated, the preheating temperature is controlled at 360°C-380°C, firstly, the blank is degreased to remove surface impurities, secondly, the blank is pre-oxidized to ensure a uniform carburized layer, and finally the blank is It can slow down the heating speed, reduce the unevenness of heating temperature and stress at different positions of different blanks, and reduce the deformation of heat treatment;
[0047] Step 2) Heating and heat preservation. The continuous heating temperature is c
PUM
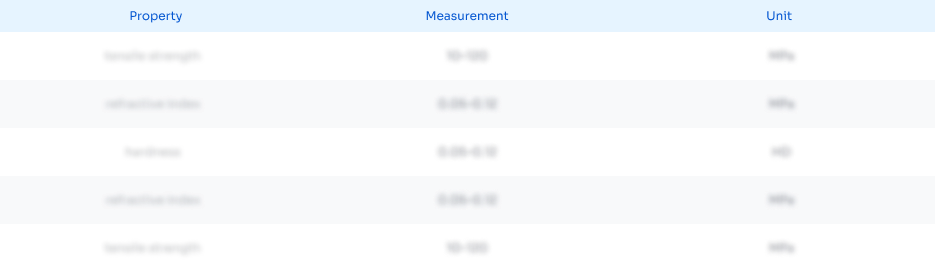
Abstract
Description
Claims
Application Information
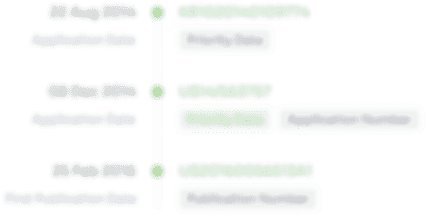
- R&D Engineer
- R&D Manager
- IP Professional
- Industry Leading Data Capabilities
- Powerful AI technology
- Patent DNA Extraction
Browse by: Latest US Patents, China's latest patents, Technical Efficacy Thesaurus, Application Domain, Technology Topic.
© 2024 PatSnap. All rights reserved.Legal|Privacy policy|Modern Slavery Act Transparency Statement|Sitemap