Heat processing technology method of austenitic ductile iron wear-resistant casting
A process method, austerite technology, applied in the field of material processing, can solve the problems of unfavorable environment and high production cost, and achieve the effects of reducing production cost, fast cooling speed and high hardness
- Summary
- Abstract
- Description
- Claims
- Application Information
AI Technical Summary
Benefits of technology
Problems solved by technology
Method used
Examples
Embodiment Construction
[0012] The heat treatment process is the key technology in the production process of the austeric ductile iron wear-resistant casting. The present invention uses a water-soluble quenching agent to carry out isothermal quenching treatment on the wear-resistant casting. Heating in a resistance furnace to 850°C-920°C, keeping it warm for 1-1.5 hours, then quickly quenching into a water-soluble quenching agent solution at a temperature of 40-60°C for 2-3 minutes, the water-soluble quenching agent consists of the following mass percentages Composition: Polyether 30%, Triethanolamine 6%, Industrial Sodium Silicate 15%, CaCl 2 10%, the balance water, wherein the molecular weight of the polyether is 40000-50000. After quenching, the surface temperature of the ausferitic ductile iron wear-resistant casting is controlled at 200-260°C. After the above-mentioned ausferitic ductile iron wear-resistant casting is taken out, it is immediately sent to the tempering furnace for isothermal temperi
PUM
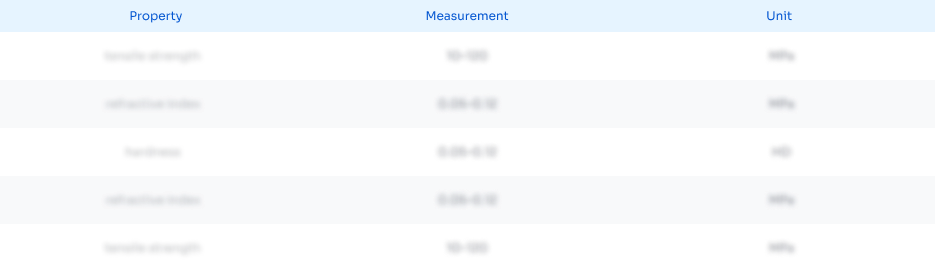
Abstract
Description
Claims
Application Information
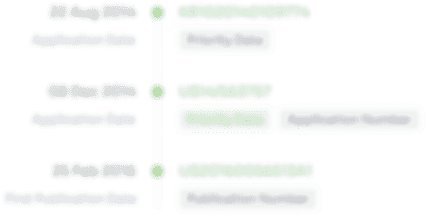
- R&D Engineer
- R&D Manager
- IP Professional
- Industry Leading Data Capabilities
- Powerful AI technology
- Patent DNA Extraction
Browse by: Latest US Patents, China's latest patents, Technical Efficacy Thesaurus, Application Domain, Technology Topic.
© 2024 PatSnap. All rights reserved.Legal|Privacy policy|Modern Slavery Act Transparency Statement|Sitemap