Polyvinyl Chloride Resin Composition for Automotive Electric Wire, and Ultrathin-Wall Low-Voltage Electric Wire for Automobile
- Summary
- Abstract
- Description
- Claims
- Application Information
AI Technical Summary
Benefits of technology
Problems solved by technology
Method used
Examples
example 1 to example 6
[0063]In Example 1 to Example 6, use was made of a resin composition configured by compounding (A) 100 parts by weight of polyvinyl chloride (specifically, one having an average degree of polymerization of 1,300) with (B) 24 parts by weight of a trimellitic-acid-based ester plasticizer (n-TOTM), (C) 5 parts by weight of a non-lead stabilizer (specifically, a Ca / Zn-based stabilizer), (D) 5 parts by weight of a reinforcing agent (specifically, 2 parts by weight of synthetic calcium carbonate and 3 parts by weight of fine-powder silica), (E) 3 parts by weight of an impact absorber (specifically, MBS (methyl methacrylate / butadiene / styrene)), and (F) 0.7 parts by weight of a processing aid (specifically, 0.5 parts by weight of PMMA (methyl methacrylate copolymer) and 0.2 parts by weight of a polyethylene wax). In Example 1 to Example 3, an electric wire having a size of 0.35 mm2 was coated with the resin composition in thicknesses of 0.15 mm, 0.20 mm, and 0.25 mm, respectively, to con
example 7 and example 8
[0077]In Example 7 and Example 8, use was made of a resin composition configured by compounding (A) 100 parts by weight of polyvinyl chloride (specifically, one having an average degree of polymerization of 1,300) with (B) 26 parts by weight of a trimellitic-acid-based ester plasticizer (n-TOTM), (C) 5 parts by weight of a non-lead stabilizer (specifically, a Ca / Zn-based stabilizer), (D) 5 parts by weight of a reinforcing agent (specifically, 2 parts by weight of synthetic calcium carbonate and 3 parts by weight of fine-powder silica), (E) 3 parts by weight of an impact absorber (specifically, MBS (methyl methacrylate / butadiene / styrene)), and (F) 0.7 parts by weight of a processing aid (specifically, 0.5 parts by weight of PMMA (methyl methacrylate copolymer) and 0.2 parts by weight of a polyethylene wax). In Example 7, an electric wire having a size of 0.35 mm2 was coated with the resin composition in a thickness of 0.15 mm to configure an insulated electric wire. In Example 8,
example 9 and example 10
[0096]In Example 9 and Example 10, use was made of a resin composition configured by compounding (A) 100 parts by weight of polyvinyl chloride (specifically, one having an average degree of polymerization of 1,300) with (B) 25 parts by weight of a trimellitic-acid-based ester plasticizer (n-TOTM), (C) 5 parts by weight of a non-lead stabilizer (specifically, a Ca / Zn-based stabilizer), (D) 5 parts by weight of a reinforcing agent (specifically, 2 parts by weight of synthetic calcium carbonate and 3 parts by weight of fine-powder silica), (E) 3 parts by weight of an impact absorber (specifically, MBS (methyl methacrylate / butadiene / styrene)), and (F) 0.7 parts by weight of a processing aid (specifically, 0.5 parts by weight of PMMA (methyl methacrylate copolymer) and 0.2 parts by weight of a polyethylene wax). In Example 9, an electric wire having a size of 0.35 mm2 was coated with the resin composition in a thickness of 0.20 mm to configure an insulated electric wire. In Example 10
PUM
Property | Measurement | Unit |
---|---|---|
Temperature | aaaaa | aaaaa |
Temperature | aaaaa | aaaaa |
Temperature | aaaaa | aaaaa |
Abstract
Description
Claims
Application Information
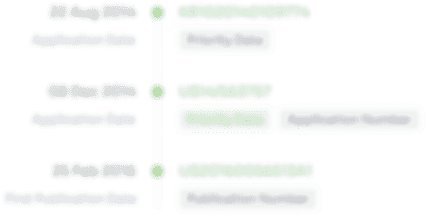
- R&D Engineer
- R&D Manager
- IP Professional
- Industry Leading Data Capabilities
- Powerful AI technology
- Patent DNA Extraction
Browse by: Latest US Patents, China's latest patents, Technical Efficacy Thesaurus, Application Domain, Technology Topic.
© 2024 PatSnap. All rights reserved.Legal|Privacy policy|Modern Slavery Act Transparency Statement|Sitemap