Heat treatment process for lowering yield ratio of ultra-high-strength marine steel
An ultra-high-strength, marine steel technology, applied in the field of ultra-high-strength marine steel heat treatment, can solve the problem of reducing the yield-strength ratio and high yield-strength ratio of ultra-high-strength marine steel, and achieve lower yield ratio and lower yield. Intensity, high intensity effect
- Summary
- Abstract
- Description
- Claims
- Application Information
AI Technical Summary
Benefits of technology
Problems solved by technology
Method used
Examples
Embodiment 1
[0019] This embodiment is a heat treatment process for reducing the yield ratio of ultra-high-strength marine steel, using critical temperature quenching + high temperature short-time tempering, that is, the quenching temperature is Ac3±20°C, and the holding time is 1.4-1.8min / mm; The tempering temperature is Ac1?(120-150)℃, and the holding time is 0.5-1.0min / mm; the quenching heating is carried out in the normalization furnace, and the water cooling process is completed, and the tempering heating is carried out in the tempering furnace, and the air cooling process completed. The tensile and impact properties of the ultra-high-strength marine steel produced in this embodiment meet the requirements of classification societies and GB712-2011, and the yield ratio is 0.91-0.93.
Embodiment 2
[0021] This embodiment is a manufacturing method of a heat treatment process for reducing the yield ratio of ultra-high-strength marine steel, which adopts critical temperature quenching + high temperature short-time tempering, that is, the quenching temperature is Ac3±20°C, and the holding time is 1.4-1.8min / mm; tempering temperature is Ac1? (100-120) ℃, holding time is 1.0-1.5min / mm; quenching heating is carried out in the normalization furnace, the water cooling process is completed, and tempering heating is carried out in the tempering furnace , completed during air cooling. The tensile and impact properties of the ultra-high-strength marine steel produced in this embodiment meet the requirements of classification societies and GB712-2011, and the yield ratio is 0.90-0.920.
Embodiment 3
[0023] This embodiment is a manufacturing method of a heat treatment process for reducing the yield ratio of ultra-high-strength marine steel, which adopts critical temperature quenching + high temperature short-time tempering, that is, the quenching temperature is Ac3±20°C, and the holding time is 1.4-1.8min / mm; tempering temperature is Ac1? (80-100) ℃, holding time is 1.5-2.0min / mm; quenching heating is carried out in the normalization furnace, the water cooling process is completed, and tempering heating is carried out in the tempering furnace , completed during air cooling. The tensile and impact properties of the ultra-high-strength marine steel produced in this embodiment meet the requirements of classification societies and GB712-2011, and the yield ratio is 0.88-0.91.
[0024]The ultra-high-strength marine steel with low yield ratio produced in Example 1-3 is quenched at critical temperature + tempered at high temperature for a short time, that is, the quenching temp
PUM
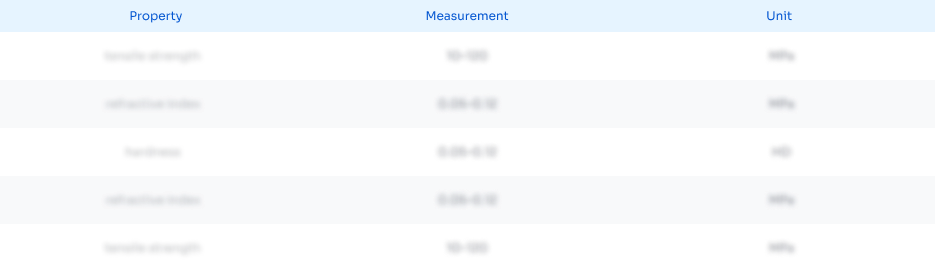
Abstract
Description
Claims
Application Information
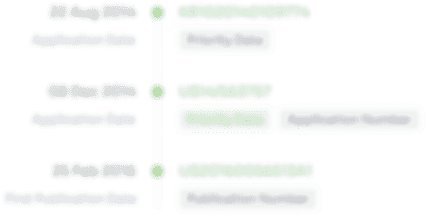
- R&D Engineer
- R&D Manager
- IP Professional
- Industry Leading Data Capabilities
- Powerful AI technology
- Patent DNA Extraction
Browse by: Latest US Patents, China's latest patents, Technical Efficacy Thesaurus, Application Domain, Technology Topic.
© 2024 PatSnap. All rights reserved.Legal|Privacy policy|Modern Slavery Act Transparency Statement|Sitemap