Manufacturing method for textured paint decorated prefab coiled material for building external wall
A technology for building exterior walls and textured paint, which is applied in the direction of architecture, building elements, and building structures, and can solve problems such as prolonged construction period, cracks in the decorative layer, and increased quality, so as to improve compactness and strength, and impervious and waterproof Good performance, good adhesion effect
- Summary
- Abstract
- Description
- Claims
- Application Information
AI Technical Summary
Problems solved by technology
Method used
Image
Examples
Example Embodiment
[0024] Example 1:
[0025] Such as figure 1 As shown, a prefabricated roll material with texture paint for building exterior walls includes an organic polymer non-woven fabric bearing layer 1, a flexible substrate layer 2 is arranged on the organic polymer non-woven fabric bearing layer 1, and the flexible substrate layer 2 Spray a waterproof primer layer 3 on the waterproof primer layer 3, set a texture paint main paint layer 4 on the waterproof primer layer 3, and set a topcoat paint layer 5 on the texture paint main paint layer 4. Such as figure 2 As shown, step surfaces 6 are provided on the edges of both sides of the prefabricated coil material decorated with texture paint for exterior walls of the building, and the step surface 6 on one side is set on the top surface of the prefabricated coil material decorated with texture paint for exterior wall of the building, and the steps on the other side The surface 6 is set on the bottom surface of the prefabricated coil material de
Example Embodiment
[0040] Example 2:
[0041] The similarities between this embodiment and Embodiment 1 will not be repeated here. The difference is: the preparation of the flexible substrate layer: A polyvinyl acetate homopolymer emulsion is used for the A emulsion, and a styrene butadiene emulsion is used for the B emulsion. The tough base material layer includes the following components in parts by weight (the total dry matter is 1000 parts): 265 parts of sub-nano nickel-iron blast furnace slag ultrafine powder; 452 parts of quartz sand from 80 mesh to 150 mesh; 52.5R silicate 235 parts of cement; 1 part of hydroxypropyl methylcellulose; 130 parts of 30% solid content polyvinyl acetate homopolymer emulsion; 40 parts of 20% solid content styrene-butadiene emulsion; 125 parts of water.
[0042] Table 2 is the relevant performance test data of the tough substrate in Example 2: Table 2
[0043]
[0044] It can meet production preparation and end product quality requirements. Part of the flexibility and i
Example Embodiment
[0045] Example 3
[0046] The similarities between this embodiment and Embodiment 1 will not be repeated here. The difference is that the preparation of the flexible substrate layer A emulsion is a polyurethane emulsion, and the B emulsion is a vinyl acetate and acrylate copolymer emulsion. The flexible substrate layer includes the following components in parts by weight (the total dry matter is 1000 parts):
[0047] 240 parts of sub-nano nickel iron blast furnace slag superfine powder;
[0048] 458 parts of quartz sand from 80 mesh to 150 mesh;
[0049] 260 shares of 52.5R Portland cement;
[0050] 1.2 parts of hydroxypropyl methylcellulose;
[0051] 80 parts of 30% solid content polyurethane emulsion;
[0052] 70 parts of 24% solid content vinyl acetate and acrylate copolymer emulsion;
[0053] 137 parts of water.
[0054] Table 3 shows the relevant performance test data of the tough substrate in Example 3: Table 3
[0055]
[0056] It can meet production preparation and end product quality
PUM
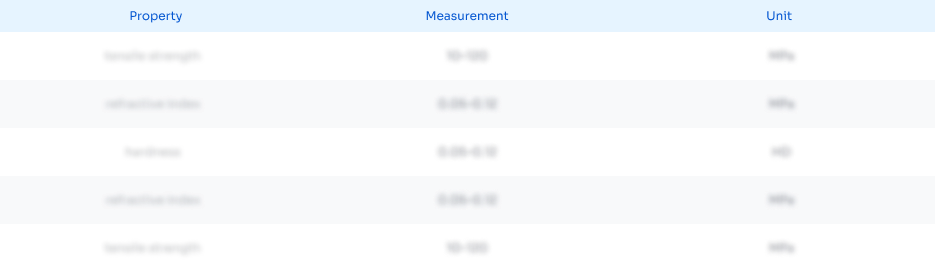
Abstract
Description
Claims
Application Information
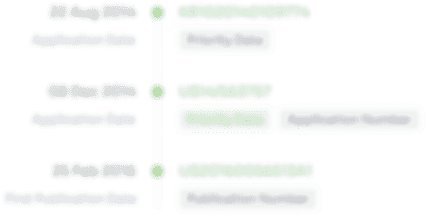
- R&D Engineer
- R&D Manager
- IP Professional
- Industry Leading Data Capabilities
- Powerful AI technology
- Patent DNA Extraction
Browse by: Latest US Patents, China's latest patents, Technical Efficacy Thesaurus, Application Domain, Technology Topic.
© 2024 PatSnap. All rights reserved.Legal|Privacy policy|Modern Slavery Act Transparency Statement|Sitemap