Baking-free pavior brick and preparation method thereof
A technology for paving bricks and clay, applied in sustainable waste treatment, solid waste management, climate sustainability, etc., can solve problems such as waste of manpower and material resources, air environment damage, hand freeze cracking, etc., to save production costs and land. resources, the effect of reducing cement usage
- Summary
- Abstract
- Description
- Claims
- Application Information
AI Technical Summary
Problems solved by technology
Method used
Examples
preparation example Construction
[0050] A kind of preparation method of unfired pavement brick provided on the one hand, the preparation method of described unfired pavement brick comprises the steps:
[0051] Step (1): Prepare blank
[0052] Take fly ash, waste pottery clay, silica fume, sodium metaaluminate, air-floated algae residue, binder and gelling agent according to the parts by weight, mix the materials and add 12-15% by weight of water and stir evenly, after 2-3 Obtain blanks for pressure forming after hours of blanking;
[0053] Step (2): Body forming
[0054] The above-mentioned uniformly mixed and trapped blank is formed into a green body with a hydraulic press, the forming pressure of the green body is 41-47MPa, and the pressurization rate is 7KN / s;
[0055] Step (3): Preparation of product
[0056] After forming, the body is cured in a curing room with a temperature of 25±1°C and a humidity of 80±1% for 29 days, and then dried naturally at room temperature to obtain a finished brick.
[0057
Embodiment 1
[0068] One aspect of this embodiment provides a burn-free pavement brick, which includes the following components in parts by weight: 15 parts of fly ash, 30 parts of waste clay, 9.2 parts of silicon powder, 2 parts of sodium metaaluminate 9 parts, 9 parts of air floating algae residue, 0.03 part of binder and 0.18 part of gelling agent.
[0069] The fineness of the waste clay is 120-180 mesh.
[0070] The gelling agent is a gelling material.
[0071] The fineness of the silicon powder is 180-200 mesh.
[0072] The pretreatment method of described waste clay is:
[0073] (1) Recycling, pre-selecting, purifying, storing and air-drying the discarded pottery clay to constant weight;
[0074] (2) Perform petrographic analysis on the discarded pottery clay obtained in step (1);
[0075] (3) Conduct a fineness test on the discarded pottery clay obtained in step (2).
[0076] A kind of preparation method of unfired pavement brick provided on the one hand, the preparation method of
Embodiment 2
[0084] One aspect of this embodiment provides a non-burning pavement brick, which includes the following components in parts by weight: 10 parts of fly ash, 47 parts of waste clay, 6.5 parts of silicon powder, and 6 parts of sodium metaaluminate. 4 parts, 4 parts of air floating algae residue, 2.7 parts of binder and 0.02 part of gelling agent.
[0085] The fineness of the waste clay is 120-180 mesh.
[0086] The gelling agent is a gelling material.
[0087] The fineness of the silicon powder is 180-200 mesh.
[0088] The pretreatment method of described waste clay is:
[0089] (1) Recycling, pre-selecting, purifying, storing and air-drying the discarded pottery clay to constant weight;
[0090] (2) Perform petrographic analysis on the discarded pottery clay obtained in step (1);
[0091] (3) Conduct a fineness test on the discarded pottery clay obtained in step (2).
[0092] A kind of preparation method of unfired pavement brick provided on the one hand, the preparation met
PUM
Property | Measurement | Unit |
---|---|---|
Compressive strength | aaaaa | aaaaa |
Fineness | aaaaa | aaaaa |
Fineness | aaaaa | aaaaa |
Abstract
Description
Claims
Application Information
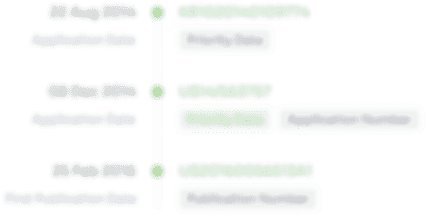
- R&D Engineer
- R&D Manager
- IP Professional
- Industry Leading Data Capabilities
- Powerful AI technology
- Patent DNA Extraction
Browse by: Latest US Patents, China's latest patents, Technical Efficacy Thesaurus, Application Domain, Technology Topic.
© 2024 PatSnap. All rights reserved.Legal|Privacy policy|Modern Slavery Act Transparency Statement|Sitemap