Double shaft furnace system and method for joint production
A combined production and shaft furnace technology, applied in the field of metallurgy, can solve problems such as reducing the comprehensive utilization rate of reducing gas, increasing the requirements for preparing reducing gas, and energy utilization, so as to improve energy utilization, reduce equipment complexity, and improve production. effect of ability
- Summary
- Abstract
- Description
- Claims
- Application Information
AI Technical Summary
Benefits of technology
Problems solved by technology
Method used
Image
Examples
Embodiment 1
[0072] Vanadium-titanium-magnetite pellets are put into the first shaft furnace 10 , and iron concentrate pellets are put into the second shaft furnace 20 . Fresh reducing gas and hydrogen-rich gas are mixed in the first mixing tank 11 to make the mixed gas composition reach H 2 With a volume ratio of 5 to CO, the effective reducing gas (H 2 +CO) volume ratio higher than 0.95. The mixed gas is passed into the first compressor 12 to make the pressure of the mixed gas reach 0.8MPa, and then passed into the heating furnace 13 for heating, so that the temperature reaches 1100°C. The heated mixed gas passes into the first shaft furnace 10 and reacts in the first shaft furnace 10 to generate vanadium-titanium sponge iron and the first top gas. The first furnace top gas pressure is 0.7MPa. Through the dry dust removal system 14, the conversion system 17 and the first CO 2 The hydrogen-rich gas is obtained after treatment by the remover 18 . Send part of the hydrogen-rich gas back t
Embodiment 2
[0076] Vanadium-titanium-magnetite pellets are put into the first shaft furnace 10 , and iron concentrate pellets are put into the second shaft furnace 20 . Fresh reducing gas and hydrogen-rich gas are mixed in the first mixing tank 11 to make the mixed gas composition reach H 2 With a volume ratio of 5 to CO, the effective reducing gas (H 2 +CO) volume ratio higher than 0.90. The mixed gas is passed into the first compressor 12 to make the pressure of the mixed gas reach 0.7 MPa, and then passed into the heating furnace 13 for heating so that the temperature thereof reaches 1050°C. The heated mixed gas passes into the first shaft furnace 10 and reacts in the first shaft furnace 10 to generate vanadium-titanium sponge iron and the first top gas. The first furnace top gas pressure is 0.65MPa. Through the dry dust removal system 14, the conversion system 17 and the first CO 2 The hydrogen-rich gas is obtained after treatment by the remover 18 . Send part of the hydrogen-rich g
Embodiment 3
[0080] Vanadium-titanium-magnetite pellets are put into the first shaft furnace 10 , and iron concentrate pellets are put into the second shaft furnace 20 . Fresh reducing gas and hydrogen-rich gas are mixed in the first mixing tank 11 to make the mixed gas composition reach H 2 With a volume ratio of 4 to CO, the effective reducing gas (H 2 +CO) volume ratio higher than 0.95. The mixed gas is passed into the first compressor 12 to make the pressure of the mixed gas reach 0.4MPa, and then passed into the heating furnace 13 for heating, so that the temperature reaches 1000°C. The heated mixed gas passes into the first shaft furnace 10 and reacts in the first shaft furnace 10 to generate vanadium-titanium sponge iron and the first top gas. The first furnace top gas pressure is 0.3MPa. Through the dry dust removal system 14, the conversion system 17 and the first CO 2 The hydrogen-rich gas is obtained after treatment by the remover 18 . Send part of the hydrogen-rich gas back t
PUM
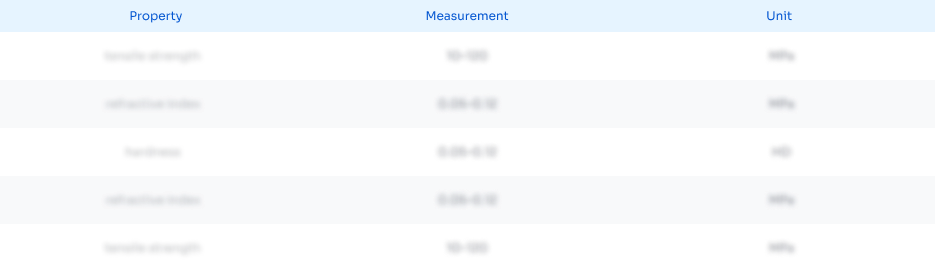
Abstract
Description
Claims
Application Information
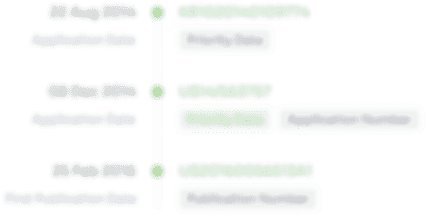
- R&D Engineer
- R&D Manager
- IP Professional
- Industry Leading Data Capabilities
- Powerful AI technology
- Patent DNA Extraction
Browse by: Latest US Patents, China's latest patents, Technical Efficacy Thesaurus, Application Domain, Technology Topic.
© 2024 PatSnap. All rights reserved.Legal|Privacy policy|Modern Slavery Act Transparency Statement|Sitemap