Heat-resistant aluminum alloy processing technology
A processing technology, aluminum alloy technology, applied in the field of heat-resistant aluminum alloy processing technology, can solve environmental pollution and other problems, achieve high melting point, improve high temperature strength, and small size
- Summary
- Abstract
- Description
- Claims
- Application Information
AI Technical Summary
Benefits of technology
Problems solved by technology
Method used
Image
Examples
Embodiment 1
[0019] A heat-resistant aluminum alloy processing technology, the method comprises the following steps:
[0020] Step 1. Weigh 24 parts of Mg, 4.2 parts of Mn, 3.2 parts of Fe, 1.6 parts of Cr, 3 parts of Zr, and 48 parts of Al as melting materials, put the melting materials into a vacuum induction furnace for smelting, preheat at 400°C for 4 hours, The temperature of the alloy liquid is controlled at 750°C during melting, and electromagnetic stirring is performed every 30 minutes;
[0021] Step 2, adding refining agent hexachloroethane to the alloy liquid in the above steps, the addition amount is 1.5% of the total weight of the alloy, and the time interval of electromagnetic stirring is 10min;
[0022] Step 3, import the alloy liquid refined in the above steps into the filter box through the ceramic foam filter plate, and set it at 700°C;
[0023] Step 4, the alloy liquid in the filter box of the above step is cast through water-cooled semi-continuous casting, and the alloy li
Embodiment 2
[0032] Weigh 20 parts of Mg, 2.1 parts of Mn, 3.2 parts of Fe, 1.6 parts of Cr, 3 parts of Zr, and 48 parts of Al as smelting materials, put the smelting materials into a vacuum induction furnace for smelting, preheat at 400°C for 4 hours, and the alloy The liquid temperature was controlled at 750° C., and electromagnetic stirring was performed every 30 minutes; the rest of the steps were the same as in Example 1.
Embodiment 3
[0034] Weigh 19 parts of Mg, 1.2 parts of Mn, 3.2 parts of Fe, 1.0 parts of Cr, 3 parts of Zr, and 48 parts of Al as melting materials, put the melting materials into a vacuum induction furnace for smelting, preheat at 400°C for 4 hours, and the alloy The liquid temperature was controlled at 750° C., and electromagnetic stirring was performed every 30 minutes; the rest of the steps were the same as in Example 1.
PUM
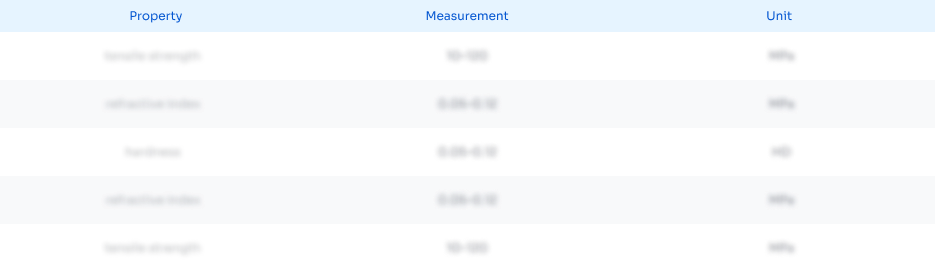
Abstract
Description
Claims
Application Information
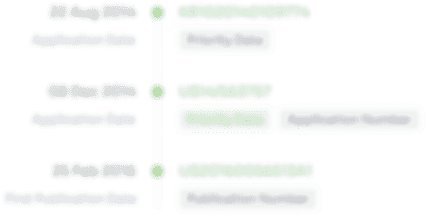
- R&D Engineer
- R&D Manager
- IP Professional
- Industry Leading Data Capabilities
- Powerful AI technology
- Patent DNA Extraction
Browse by: Latest US Patents, China's latest patents, Technical Efficacy Thesaurus, Application Domain, Technology Topic.
© 2024 PatSnap. All rights reserved.Legal|Privacy policy|Modern Slavery Act Transparency Statement|Sitemap