Monocrystalline silicon surface composite microstructure based on full-wave band anti-reflection and a preparation method thereof
A technology of surface compounding and monocrystalline silicon, applied in the field of photovoltaics, can solve the problems such as the inability to realize the utilization of long-wavelength solar energy, and achieve the effects of improving utilization, improving conversion efficiency, and optimizing structure
- Summary
- Abstract
- Description
- Claims
- Application Information
AI Technical Summary
Problems solved by technology
Method used
Examples
Example Embodiment
[0038] Such as figure 1 Shown is a flowchart of the present invention. The preparation method of a single crystal silicon surface composite microstructure based on full-band antireflection of the present invention includes some or all of the following steps (1) to (4), wherein each step is performed one or more times;
[0039] (1) Silicon-based mask: Hydrophilic treatment of silicon wafers, preparation of a mixed solution of polystyrene beads, masking of the hydrophilic-treated silicon wafers, use a propelling syringe to lay, and drip sodium lauryl sulfate Solution, and use the lifting method to complete the mask, and then air-dry the mask naturally, and then vacuum dry for 3 to 5 hours, and lay polystyrene pellets on the surface of the silicon wafer;
[0040] Preferably, the steps of the hydrophilic treatment of the silicon wafer are: taking single crystal silicon, cleaning, cutting samples; placing it in a mixed solution of concentrated sulfuric acid and hydrogen peroxide, and heati
Example Embodiment
[0052] Example 1: Preparation of a mixed diameter nano-pillar array structure.
[0053] Select 100mm×100mm round double-sided polished P-type monocrystalline silicon, slice it with a diamond wafer knife, and make a 25mm×25mm square silicon wafer substrate; mix the silicon wafer with concentrated sulfuric acid and hydrogen peroxide with a mass ratio of 7:3 Heat the solution in a heat bath at 90°C for one hour to complete the hydrophilic treatment; prepare a mixed solution of polystyrene (Polystyrene, abbreviated PS) beads: PS beads solution with a particle size of 400nm, PS beads solution with a particle size of 600nm, deionized Water and absolute ethanol are mixed in a volume ratio of 0.5:0.5:3:7, and the mixture is ultrasonically shaken at room temperature for 5 minutes; to prepare a sodium dodecyl sulfate (SDS) solution: take 1 g of sodium dodecyl sulfate and put it in Dissolve in 20mL of deionized water by ultrasonically shaking for 20 minutes; take a 9mm×9mm round petri dish, po
Example Embodiment
[0054] Example 2: Preparation of a mixed diameter nano pencil array structure.
[0055] Select 100mm×100mm round double-sided polished P-type monocrystalline silicon, slice it with a diamond wafer knife, and make a 25mm×25mm square silicon wafer substrate; mix the silicon wafer with concentrated sulfuric acid and hydrogen peroxide with a mass ratio of 7:3 Place the solution in a heat bath at a temperature of 90°C for one hour to complete the hydrophilic treatment; prepare a mixed solution of polystyrene (Polystyrene, abbreviated PS) beads: a solution of nmPS beads with a particle size of 400, a solution of nmPS beads with a particle size of 600, and Ionized water and absolute ethanol were mixed in a volume ratio of 0.5:0.5:3:7, and the solution was sonicated at room temperature for 5 minutes; to prepare a sodium dodecyl sulfate (SDS) solution: take 1 gram of sodium dodecyl sulfate and put it in Dissolve in 20mL of deionized water by ultrasonically shaking for 20 minutes; take a 9mm×
PUM
Property | Measurement | Unit |
---|---|---|
Film thickness | aaaaa | aaaaa |
Film thickness | aaaaa | aaaaa |
Particle size | aaaaa | aaaaa |
Abstract
Description
Claims
Application Information
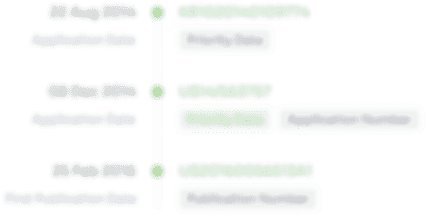
- R&D Engineer
- R&D Manager
- IP Professional
- Industry Leading Data Capabilities
- Powerful AI technology
- Patent DNA Extraction
Browse by: Latest US Patents, China's latest patents, Technical Efficacy Thesaurus, Application Domain, Technology Topic.
© 2024 PatSnap. All rights reserved.Legal|Privacy policy|Modern Slavery Act Transparency Statement|Sitemap