Composite heat dissipation material
A composite heat dissipation material and combined technology, applied in the direction of layered products, chemical instruments and methods, metal layered products, etc., can solve the problems of high cost, achieve low cost, prolong upward heat penetration time, and low external surface temperature Effect
- Summary
- Abstract
- Description
- Claims
- Application Information
AI Technical Summary
Benefits of technology
Problems solved by technology
Method used
Image
Examples
Embodiment Construction
[0024] The present invention will be further described in detail below in conjunction with the accompanying drawings and specific embodiments.
[0025] attached figure 1 It is the first embodiment of the composite heat dissipation material according to the present invention, which includes a graphite composite layer (not marked); the graphite composite layer includes at least two graphite layers 1; adjacent graphite layers 1 pass through The adhesive layer 2 is directly bonded together; the outer side of the graphite composite layer is provided with a heat penetration reducing layer 3; the thermal penetration reducing layer 3 and the graphite composite layer are provided with an adhesive layer 2 .
[0026] The heat penetration reducing layer 3 can be one layer; it can also be multi-layer stacked together, and the adjacent layers are in direct contact or bonded together through an adhesive layer or provided with gaps.
[0027] The graphite layer 1 is composed of natural graphite
PUM
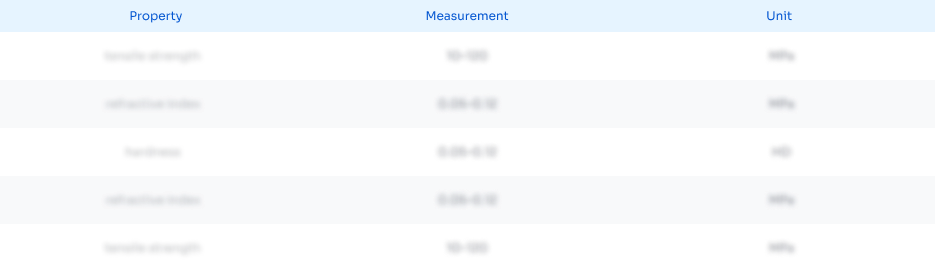
Abstract
Description
Claims
Application Information
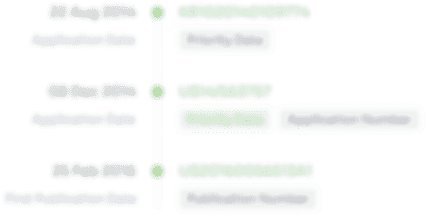
- R&D Engineer
- R&D Manager
- IP Professional
- Industry Leading Data Capabilities
- Powerful AI technology
- Patent DNA Extraction
Browse by: Latest US Patents, China's latest patents, Technical Efficacy Thesaurus, Application Domain, Technology Topic.
© 2024 PatSnap. All rights reserved.Legal|Privacy policy|Modern Slavery Act Transparency Statement|Sitemap