Energy-saving and environment-friendly high-strength epoxy resin concrete material
An epoxy resin, energy-saving and environment-friendly technology, applied in the field of construction concrete, can solve the problems of toughness and resistance to be improved, environmental protection, high production cost, etc., and achieve the effects of easy promotion and use, high production efficiency and low production cost
- Summary
- Abstract
- Description
- Claims
- Application Information
AI Technical Summary
Problems solved by technology
Method used
Image
Examples
Embodiment 1
[0025] The invention provides an energy-saving and environment-friendly high-strength epoxy resin concrete material, wherein the main materials used include by weight: 70 parts of epoxy resin, 30 parts of base material, 8 parts of river sand and 10 parts of asbestos fiber. The auxiliary materials include by weight: 10 parts of corn starch, 8 parts of reactive diluent, 2 parts of defoamer, 15 parts of curing agent, and 6 parts of toughening agent.
[0026] Preferably, the base material is made by mixing gangue and limestone, and the mass ratio of gangue to limestone is set to 10:6.
[0027] Preferably, the epoxy resin is set to be glycidyl ester epoxy resin, and the curing agent is set to be diaminodiphenyl sulfone.
[0028] Preferably, the reactive diluent is set to propylene oxide phenyl ether, the toughening agent is set to aralkyl ether, and the defoamer is set to polyether modified silicone.
[0029] An energy-saving and environment-friendly high-strength epoxy resin concret
Embodiment 2
[0037] The invention provides an energy-saving and environment-friendly high-strength epoxy resin concrete material, wherein the main materials used include by weight: 80 parts of epoxy resin, 35 parts of base material, 10 parts of river sand and 12 parts of asbestos fiber. The auxiliary materials include by weight: 11 parts of cornstarch, 9 parts of reactive diluent, 3 parts of defoamer, 18 parts of curing agent, and 7 parts of toughening agent.
[0038] Preferably, the base material is made by mixing gangue and limestone, and the mass ratio of gangue to limestone is set to 12:5.
[0039] Preferably, the epoxy resin is set to be glycidyl ester epoxy resin, and the curing agent is set to be diaminodiphenyl sulfone.
[0040]Preferably, the reactive diluent is set to propylene oxide phenyl ether, the toughening agent is set to aralkyl ether, and the defoamer is set to polyether modified silicone.
[0041] An energy-saving and environment-friendly high-strength epoxy resin concrete
Embodiment 3
[0049] The invention provides an energy-saving and environment-friendly high-strength epoxy resin concrete material, wherein the main materials used include by weight: 90 parts of epoxy resin, 35 parts of base material, 10 parts of river sand and 14 parts of asbestos fiber. The auxiliary materials include by weight: 11 parts of cornstarch, 9 parts of reactive diluent, 3 parts of defoamer, 22 parts of curing agent, and 7 parts of toughening agent.
[0050] Preferably, the base material is made by mixing gangue and limestone, and the mass ratio of gangue to limestone is set to 14:5.
[0051] Preferably, the epoxy resin is set to glycidyl ester epoxy resin, and the curing agent is set to m-aminomethylamine.
[0052] Preferably, the reactive diluent is polyglycidol, the toughening agent is aralkyl ether, and the defoamer is polyether-modified silicone.
[0053] An energy-saving and environment-friendly high-strength epoxy resin concrete material also includes a method for preparing
PUM
Property | Measurement | Unit |
---|---|---|
Diameter | aaaaa | aaaaa |
Diameter | aaaaa | aaaaa |
Diameter | aaaaa | aaaaa |
Abstract
Description
Claims
Application Information
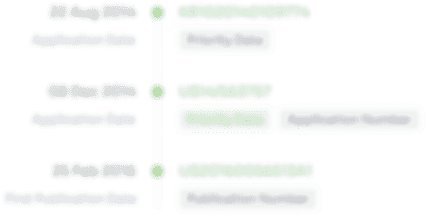
- R&D Engineer
- R&D Manager
- IP Professional
- Industry Leading Data Capabilities
- Powerful AI technology
- Patent DNA Extraction
Browse by: Latest US Patents, China's latest patents, Technical Efficacy Thesaurus, Application Domain, Technology Topic.
© 2024 PatSnap. All rights reserved.Legal|Privacy policy|Modern Slavery Act Transparency Statement|Sitemap