Composition for forming hard coating layer, method of preparing hard coating film and the hard coating film prepared by using the same
A hard coating and composition technology, applied in the field of hard coating forming compositions, can solve the problems of curling, insufficient flexibility, difficulty in achieving high hardness, etc., to prevent cracks or curling, improve hardness and curl inhibition characteristics , the effect of shortening the curing half-life
- Summary
- Abstract
- Description
- Claims
- Application Information
AI Technical Summary
Problems solved by technology
Method used
Image
Examples
Embodiment 1~14、 comparative example 1 and 2
[0193] Relative to the total weight of the composition, the epoxysiloxane resin, crosslinking agent, thermal initiator, photoinitiator and solvent prepared in the preparation example were mixed in the weight ratio of the following Table 1 to prepare a hard coat layer. combination.
[0194] The composition for forming a hard coat layer was coated on a colorless polyimide (cPI) film having a thickness of 80 μm by the Meyer rod method, and was left to stand at a temperature of 60° C. for 5 minutes.
[0195] Using a high pressure metal lamp at 1J / cm 2 UV was irradiated and then cured at a temperature of 120° C. for 15 minutes to prepare a hard coat film forming a composite cured hard coat layer having a thickness of 30 μm.
Embodiment 15 and comparative example 3
[0197] Each component was mixed according to the following Table 1, and the composition for hard-coat layer formation was prepared.
[0198] The composition for forming a hard coat layer was coated on a cPI film having a thickness of 80 μm by the Meyer rod method, and left to stand at a temperature of 60° C. for 5 minutes.
[0199] Using a high pressure metal lamp at 1J / cm 2 UV was irradiated and then cured at a temperature of 120° C. for 15 minutes to form a composite cured hard coat layer with a thickness of 20 μm.
[0200] The hard coat layer forming composition was coated on the bottom surface of the cPI film on which the composite cured hard coat layer was not formed by the Meyer rod method, and left to stand at a temperature of 60° C. for 5 minutes. Afterwards, using a high-pressure metal lamp at 1J / cm 2 UV was irradiated to form a photocurable hard coat layer with a thickness of 5 μm, thereby preparing the hard coat films of Example 15 and Comparative Example 3.
[
Embodiment 16~21
[0205] A hard coat film was prepared by the same method as in Example 15, but the thicknesses of the composite cured hard coat layer and the photocured hard coat layer were changed according to Table 2 below.
[0206] [Table 2]
[0207] distinguish Composite cured hard coat thickness (μm) Thickness of light-cured hard coat (μm) Example 15 20 5 Example 16 5 5 Example 17 5.5 5 Example 18 10 5 Example 19 30 5 Example 20 40 5 Example 21 50 5
PUM
Property | Measurement | Unit |
---|---|---|
Thickness | aaaaa | aaaaa |
Thickness | aaaaa | aaaaa |
Thickness | aaaaa | aaaaa |
Abstract
Description
Claims
Application Information
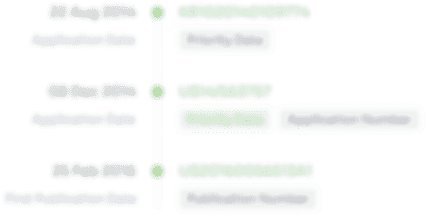
- R&D Engineer
- R&D Manager
- IP Professional
- Industry Leading Data Capabilities
- Powerful AI technology
- Patent DNA Extraction
Browse by: Latest US Patents, China's latest patents, Technical Efficacy Thesaurus, Application Domain, Technology Topic.
© 2024 PatSnap. All rights reserved.Legal|Privacy policy|Modern Slavery Act Transparency Statement|Sitemap