Pulverized coal synthesis gas and coal water slurry synthesis gas ratio conversion process and device
A technology of coal water slurry and synthesis gas, applied in the direction of mixing method, transportation and packaging, gas and gas/steam mixing, etc., can solve the problem of slow increase and decrease of catalyst bed temperature, decrease of overall energy consumption of the system, and difficulty in hydrogen and carbon regulation Major problems, to achieve the effect of reducing operation difficulty, increasing operating efficiency, and reducing energy consumption
- Summary
- Abstract
- Description
- Claims
- Application Information
AI Technical Summary
Benefits of technology
Problems solved by technology
Method used
Image
Examples
Embodiment
[0125] The flow rate of the first pulverized coal gasification synthesis gas is 615350Nm / h, the second pulverized coal gasification synthesis gas flow rate is 615350Nm / h, and the coal water slurry gasification synthesis gas flow rate is 303997.8Nm / h.
[0126] exist figure 1 In the device shown, the first pulverized coal gasification synthesis gas from the first pulverized coal gas filter is divided into three paths:
[0127] After the first pulverized coal gasification synthesis gas (10%) comes out from outlet 1 of the first pulverized coal gas filter, it passes through the first pulverized coal gas mixer and comes out with a stream of coal water from coal water slurry gas filter outlet 1. The slurry gasification synthesis gas is mixed, then heated to about 255°C by the first gas preheater, and then enters the first shift furnace, and the shift reaction is carried out at 3.92MPaG and 255°C.
[0128]The shifted gas after the first CO shift reaction, temperature: ~450°C, CO
PUM
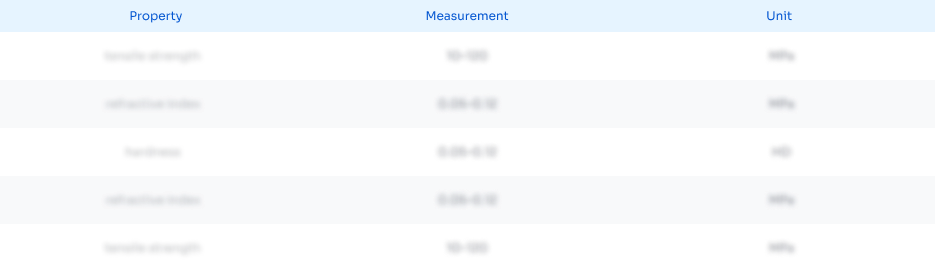
Abstract
Description
Claims
Application Information
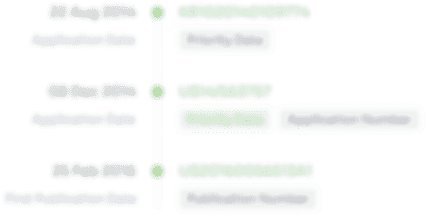
- R&D Engineer
- R&D Manager
- IP Professional
- Industry Leading Data Capabilities
- Powerful AI technology
- Patent DNA Extraction
Browse by: Latest US Patents, China's latest patents, Technical Efficacy Thesaurus, Application Domain, Technology Topic.
© 2024 PatSnap. All rights reserved.Legal|Privacy policy|Modern Slavery Act Transparency Statement|Sitemap