Force-controlled grinding method and system for adjusting speed of robot in real time
A real-time adjustment, robot technology, applied in manipulators, program-controlled manipulators, manufacturing tools, etc., can solve the problem of not being able to adjust the robot path speed, and achieve the effect of solving uneven burrs, ensuring processing quality, and improving grinding efficiency.
- Summary
- Abstract
- Description
- Claims
- Application Information
AI Technical Summary
Problems solved by technology
Method used
Image
Examples
Example Embodiment
[0050] Example 1:
[0051] According to a real-time adjustment of the robot, the power control grinding method of real-time adjustment robot speed is provided. Figure 1 - Figure 4 As shown, including:
[0052] Step S1: Set the initial grinding path and grinding force;
[0053] Step S2: Real-time processing sensor data to get contact force;
[0054] Step S3: The deviation of the contact force and the grinding force obtains a positional deviation by the inside controller;
[0055] Step S4: Adjust the speed ratio based on the contact force;
[0056] Step S5: Depending on the speed ratio, the adjusted speed is adjusted, and the adjusted speed is transferred to the position to the robot.
[0057] Specifically, in the step S2:
[0058] The quality of the grinding head, the centroid parameters are introduced to the controller, gravity compensation, gravity compensation is the process of reducing the gravity of the sensor measurement moment to obtain contact force.
[0059]Specifically, in
Example Embodiment
[0067] Example 2:
[0068] Example 2 Example 1 is the preferred embodiment, more particularly to the present invention will be described.
[0069] Power control method for real-time adjustment of the robot grinding speed skilled in the art may be provided according to the present invention, it is understood to real-time adjustment of the speed of the robot DETAILED DESCRIPTION grinding force control system, i.e., real-time adjustment of the speed of the robot grinding force control system the robot can be adjusted in real time by the speed of execution of the control flow of grinding steps of the method to be implemented.
[0070] According to a real-time adjustment of the speed of the robot grinding force control system of the present invention provides, comprising:
[0071] Module M1: set the initial grinding force and grinding path;
[0072] Module M2: real-time processing of sensor data to obtain the contact force;
[0073] Module M3: contact force and grinding force variations
Example Embodiment
[0086] Example 3:
[0087] Example 3 Example 1 is the preferred embodiment, more particularly to the present invention will be described.
[0088] Compared to the prior art, the main point of the invention is a time adjustment of the different feed rate of the grinding force of the robot, the glitch slow grinding of little thicker, thinner faster grinding burr. The main point of the invention is the speed control, and force control the gravity compensation module prior art there is no difference. As can be seen from the control map. They mainly want to solve the problem of uneven glitch.
[0089] Run step of the invention as follows:
[0090] 1, the initial grinding path, grinding force.
[0091] 2, the grinding process to give real-time sensor data processing actual contact force.
[0092] 3, the contact force and grinding force variations obtained by the position deviation admittance controller, positional deviation superimposed grinding path.
[0093] 4. The time adjustment of th
PUM
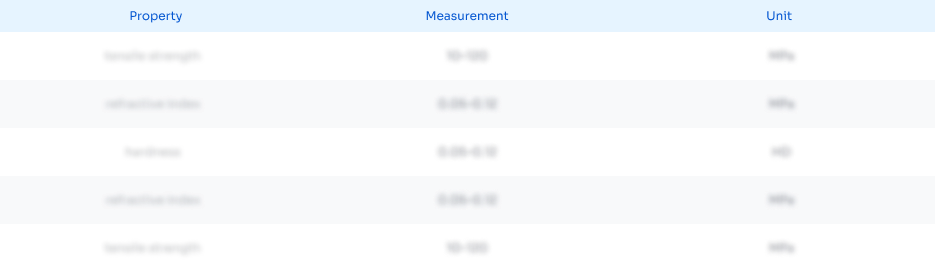
Abstract
Description
Claims
Application Information
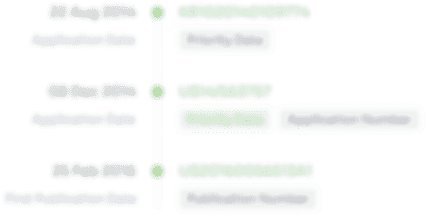
- R&D Engineer
- R&D Manager
- IP Professional
- Industry Leading Data Capabilities
- Powerful AI technology
- Patent DNA Extraction
Browse by: Latest US Patents, China's latest patents, Technical Efficacy Thesaurus, Application Domain, Technology Topic.
© 2024 PatSnap. All rights reserved.Legal|Privacy policy|Modern Slavery Act Transparency Statement|Sitemap