Preparation method of titanium/aluminum/magnesium composite plate
A composite plate and aluminum alloy plate technology, applied in welding equipment, manufacturing tools, non-electric welding equipment, etc., can solve the problems of affecting the application range, low bonding strength, poor corrosion resistance, etc., to improve mechanical properties, easy to realize, The effect of simple process
- Summary
- Abstract
- Description
- Claims
- Application Information
AI Technical Summary
Benefits of technology
Problems solved by technology
Method used
Image
Examples
Embodiment 1
[0019] In the preparation method of this embodiment, titanium alloy plates of 2 mm × 340 mm × 540 mm (thickness × width × length) and aluminum alloy plates of 1 mm × 300 mm × 500 mm (thickness × width × length) are used as flying plates, and 6 mm × 300 mm × 500 mm (Thickness×Width×Length) magnesium alloy plate is used as the substrate. Firstly, the surface of each plate is polished to remove the oxide film, and the magnesium alloy plate is placed on a flat fort to be completely bonded, and the aluminum alloy plate and titanium alloy plate are sequentially Stack it on the magnesium alloy sheet, and place an aluminum support with a height of 4mm between the adjacent sheets of the magnesium alloy sheet, aluminum alloy sheet and titanium alloy sheet, and then cover the surface of the titanium alloy sheet facing away from the substrate Plastic film, laying powdered emulsion explosive containing 10% wood chips and 20% sand by mass fraction on the plastic film, and the laying thickness o
Embodiment 2
[0023] In the preparation method of this embodiment, titanium alloy plates of 1 mm × 340 mm × 540 mm (thickness × width × length) and aluminum alloy plates of 1 mm × 300 mm × 500 mm are used as flying plates, and 10 mm × 300 mm × 500 mm (thickness × width × length) The magnesium alloy sheet is used as the substrate. Firstly, the surface of each sheet is polished to remove the oxide film, and the magnesium alloy sheet is placed on a flat fort to be completely bonded, and the aluminum alloy sheet and titanium alloy sheet are stacked on the magnesium alloy sheet in turn. , and place an aluminum support with a height of 2mm between the adjacent plates in the magnesium alloy plate, aluminum alloy plate and titanium alloy plate, and then cover the surface of the titanium alloy plate facing away from the substrate with a plastic film, and on the plastic film Lay the powdered emulsion explosive containing 10% wood chips and 20% gravel by mass fraction, and the laying thickness of the powd
Embodiment 3
[0026] In the preparation method of this embodiment, titanium alloy plates of 5 mm × 340 mm × 540 mm (thickness × width × length) and aluminum alloy plates of 1 mm × 300 mm × 500 mm (thickness × width × length) are used as flying plates, and 8 mm × 300 mm × 500 mm (Thickness×Width×Length) magnesium alloy plate is used as the substrate. Firstly, the surface of each plate is polished to remove the oxide film, and the magnesium alloy plate is placed on a flat fort to be completely bonded, and the aluminum alloy plate and titanium alloy plate are sequentially Stack it on the magnesium alloy sheet, and place an aluminum support with a height of 4mm between the adjacent sheets of the magnesium alloy sheet, aluminum alloy sheet and titanium alloy sheet, and then cover the surface of the titanium alloy sheet facing away from the substrate Plastic film, laying powdered emulsion explosive containing 10% wood chips and 20% sand on the plastic film, and the laying thickness of the powdered em
PUM
Property | Measurement | Unit |
---|---|---|
Thickness | aaaaa | aaaaa |
Thickness | aaaaa | aaaaa |
Thickness | aaaaa | aaaaa |
Abstract
Description
Claims
Application Information
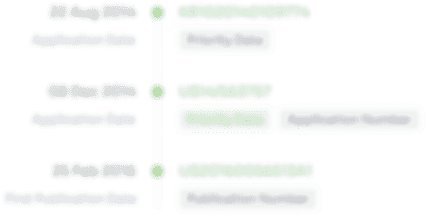
- R&D Engineer
- R&D Manager
- IP Professional
- Industry Leading Data Capabilities
- Powerful AI technology
- Patent DNA Extraction
Browse by: Latest US Patents, China's latest patents, Technical Efficacy Thesaurus, Application Domain, Technology Topic.
© 2024 PatSnap. All rights reserved.Legal|Privacy policy|Modern Slavery Act Transparency Statement|Sitemap