Method for mfg. single sheet pneumatic gel mini valve
A manufacturing method and gel technology, applied in the field of monolithic aerodynamic gel microvalve manufacturing, can solve the problems of unfavorable microfluidic systems, high requirements for operators, and high manufacturing costs of micropumps, and achieve low energy consumption for opening and promote The effect of development, simple structure
- Summary
- Abstract
- Description
- Claims
- Application Information
AI Technical Summary
Problems solved by technology
Method used
Examples
Embodiment 1
[0029] (1) The micro-replication template was obtained by rapid prototyping technology, and the silicone rubber substrate containing the pump cavity structure and microchannels was obtained by casting the silicone rubber material, as follows:
[0030] A. Rapid preparation of micro-replication template: adopt SU-850 negative photoresist (USA Micro Chem Company), spin the glue condition at 500rpm for 1 minute, obtain a photoresist with a thickness of 1000μm, and pre-bake at 85°C for 30 Minutes, 95°C for 30 minutes, exposure using MA6 lithography machine from German Karl Suss company, exposure time is 600 seconds, medium baking condition is 95°C for 30 minutes, development time is 15 minutes, and then a layer of metal with a thickness of 0.1 microns is sputtered Nickel, to obtain the required photoresist mold, the structure of which is the pump cavity structure and the convex pattern of the microchannel.
[0031] B. Replication of the template pattern: Mix Dow Corning's sylgard184A
Embodiment 2
[0049] (1) The micro-replication template was obtained by rapid prototyping technology, and the silicone rubber substrate containing the pump cavity structure and microchannels was obtained by casting the silicone rubber material, as follows:
[0050] A. Rapid preparation of micro-replication template: adopt SU-850 negative photoresist (Micro Chem Company, USA), the condition of spinning the glue is 2000rpm for 1 minute, and obtain a photoresist with a thickness of 200μm, and the pre-baking condition is 85°C for 30 Minutes, 95°C for 30 minutes, exposure using MA6 lithography machine from German Karl Suss company, exposure time is 100 seconds, medium baking condition is 95°C for 30 minutes, development time is 5 minutes, and then a layer of metal with a thickness of 0.1 microns is sputtered Nickel, to obtain the required photoresist mold, the structure of which is the pump cavity structure and the convex pattern of the microchannel.
[0051] B. Replication of the template pattern:
Embodiment 3
[0069] (1) The micro-replication template was obtained by rapid prototyping technology, and the silicone rubber substrate containing the pump cavity structure and microchannels was obtained by casting the silicone rubber material, as follows:
[0070] A. Rapid preparation of micro-replication template: use SU-850 negative photoresist (Micro Chem, USA), spin the glue at 1000rpm for 1 minute, obtain a photoresist with a thickness of 800μm, and pre-bake at 85°C for 30 Minutes, 95°C for 30 minutes, exposure using MA6 lithography machine from German Karl Suss company, exposure time is 300 seconds, medium baking condition is 95°C for 30 minutes, development time is 5 minutes, and then a layer of metal with a thickness of 0.1 microns is sputtered Nickel, to obtain the required photoresist mold, the structure of which is the pump cavity structure and the convex pattern of the microchannel.
[0071] B. Replication of the template pattern: Mix Dow Corning's sylgard184A solution and sylgard
PUM
Property | Measurement | Unit |
---|---|---|
Thickness | aaaaa | aaaaa |
Abstract
Description
Claims
Application Information
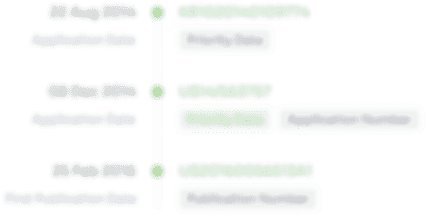
- R&D Engineer
- R&D Manager
- IP Professional
- Industry Leading Data Capabilities
- Powerful AI technology
- Patent DNA Extraction
Browse by: Latest US Patents, China's latest patents, Technical Efficacy Thesaurus, Application Domain, Technology Topic.
© 2024 PatSnap. All rights reserved.Legal|Privacy policy|Modern Slavery Act Transparency Statement|Sitemap