Viscosity Modifiers Comprising Blends of Ethylene-Based Copolymers
a copolymer and viscosity modifier technology, applied in the field of polymer blends, can solve the problems of extreme viscosity and solid formulations
- Summary
- Abstract
- Description
- Claims
- Application Information
AI Technical Summary
Problems solved by technology
Method used
Examples
specific embodiments
[0123]In one or more specific embodiments, the present invention is directed to a polymer blend composition for use as a VI improver comprising a first ethylene-based copolymer and a second ethylene-based copolymer. The first copolymer has an ethylene content from about 44 to about 52 wt %, or from about 45 to about 51 wt %, or from about 46 to about 50 wt %; the second copolymer has an ethylene content from about 68 to about 75 wt %, or from about 69 to about 74 wt %, or from about 70 to about 73 wt %. Additionally, the ethylene content of the second copolymer is at least about 17 wt %, or at least about 19 wt %, or at least about 21 wt % greater than that ethylene content of the first copolymer.
[0124]In the same or other embodiments, the first copolymer has a first melt heat of fusion from about 0 to about 15 J / g, or from about 0 to about 10 J / g, or from about 0 to about 5 J / g; the second copolymer has a first melt heat of fusion from about 40 to about 65 J / g, or from about 42 to ...
examples
Preparation of the Ethylene-Based Copolymers
[0159]A variety of ethylene-based copolymers as described above were synthesized as follows. Ethylene and propylene were polymerized in solution in a continuous stirred tank reactor, using hexane as a solvent. Polymerization in the reactor was performed at a temperature of about 110-115° C., an overall pressure of about 20 bar, and ethylene and propylene feed rates of about 1.3 and 2.0 kg / hr, respectively. N,N-dimethylanilinium tetrakis(pentafluorophenyl)boron was used to activate di(p-triethylsilylphenyl)methenyl [cyclopentadienyl)(2,7-di-tert-butylfluorophenyl)]hathium dimethyl as the catalyst. During the polymerization process, hydrogen addition and temperature control were used to achieve the desired melt flow rate. The catalyst, activated externally to the reactor, was added as needed in amounts effective to maintain the target polymerization temperature.
[0160]The copolymer solution exiting the reactor was stopped from further polymer...
examples 1-115
[0162]Polymer blend compositions were prepared comprising a first ethylene-based copolymer and a second ethylene based copolymer, both of which were selected from the polymers listed in Table 1. The blends were made by melt blending in a Brabender mixer having an internal cavity of 250 ml at a temperature of from about 120 to about 150° C. for 3 to 5 minutes using low shear blades rotating at a speed of 15 to 200 rpm. The ethylene-based copolymers were protected during the mixing operation with a nitrogen blanket and by the addition of 1000 ppm of a 3:1 mixture of Irganox 1076 and Irgafos 168 (both available from BASF Corporation) before blending. The compositions of the resulting polymer blends are set forth in Table 2 below, and the amounts of each component are given in grams.
TABLE 2Example No.A1A2A3A4B1B2B3B4B5B61160240216024031602404200200520020062002007240160824016092401601028012011280120122801201332080143208015320801616024017160240181602401920020020200200212002002224016023240...
PUM
Property | Measurement | Unit |
---|---|---|
temperature | aaaaa | aaaaa |
weight ratio | aaaaa | aaaaa |
heat of fusion | aaaaa | aaaaa |
Abstract
Description
Claims
Application Information
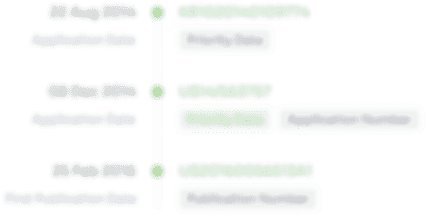
- R&D Engineer
- R&D Manager
- IP Professional
- Industry Leading Data Capabilities
- Powerful AI technology
- Patent DNA Extraction
Browse by: Latest US Patents, China's latest patents, Technical Efficacy Thesaurus, Application Domain, Technology Topic.
© 2024 PatSnap. All rights reserved.Legal|Privacy policy|Modern Slavery Act Transparency Statement|Sitemap