Arc welding method and arc welding apparatus
a technology of arc welding and arc welding, which is applied in the direction of arc welding apparatus, welding apparatus, manufacturing tools, etc., can solve the problems of failure to form the desired size globule, and achieve the effect of improving the arc-starting performan
- Summary
- Abstract
- Description
- Claims
- Application Information
AI Technical Summary
Benefits of technology
Problems solved by technology
Method used
Examples
first exemplary embodiment
[0018]FIG. 1 is a schematic diagram showing a general structure of an arc welding apparatus according to the first exemplary embodiment of this invention, and FIG. 2 is a graphic representation illustrating waveforms of wire feeding speed, welding voltage and welding current of the arc welding apparatus.
[0019]In FIG. 1, primary rectifier element 3 rectifies the power input from mains power source 1. Switching element 4 regulates an output of primary rectifier element 3 to produce an output suitable for welding. Main power transformer 2 converts the output of switching element 4 into an output suitable for welding. Secondary rectifier element 6 rectifies the output of main power transformer 2. Reactor 5 smoothes the output of secondary rectifier element 6 into a current form suitable for welding. Welding current detector 8 detects a welding current. Welding voltage detector 9 detects a welding voltage. Short / arc detector 10 determines whether welding condition is in a short mode, in ...
second exemplary embodiment
[0038]In this second exemplary embodiment, like reference marks are used to designate like structural components as those of the first exemplary embodiment, and details of them will be omitted while description will cover only different items. A main point of difference from the first exemplary embodiment is that the wire feeding speed is decelerated at a predetermined inclination from a point of time when a signal for turning off the welding power output is input. Another point of difference is that wire 16 is retracted backward for a predetermined duration of time, starting from a point when shorting occurs for the first time following the input of the signal for turning off the welding power output, or a welding end signal, so as to open the shorting and pull up wire 16 to end the welding.
[0039]There is also an alternative method as follows, instead of decelerating the wire feeding speed at the predetermined inclination from the time when the signal for turning off the welding po...
PUM
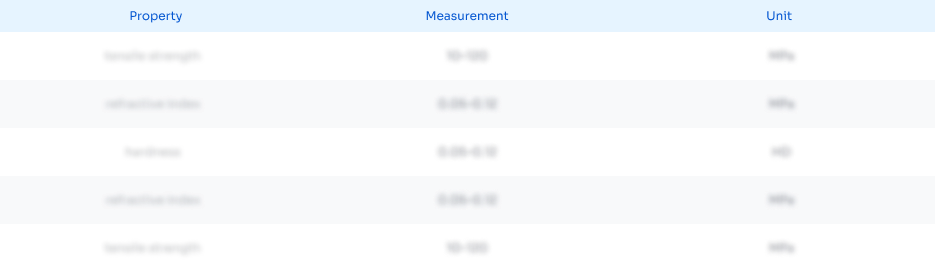
Abstract
Description
Claims
Application Information
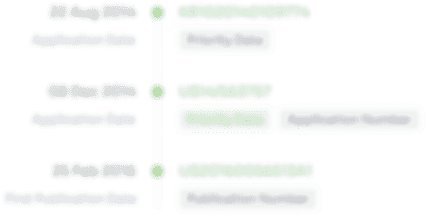
- R&D Engineer
- R&D Manager
- IP Professional
- Industry Leading Data Capabilities
- Powerful AI technology
- Patent DNA Extraction
Browse by: Latest US Patents, China's latest patents, Technical Efficacy Thesaurus, Application Domain, Technology Topic.
© 2024 PatSnap. All rights reserved.Legal|Privacy policy|Modern Slavery Act Transparency Statement|Sitemap