Catalyst for Selective Dehydrogenation / Oxidative Dehydrogenation Reactions and Process for the Preparation Thereof
- Summary
- Abstract
- Description
- Claims
- Application Information
AI Technical Summary
Benefits of technology
Problems solved by technology
Method used
Image
Examples
example 1
Synthesis of TiO2
[0074]5 ml titanium isopropoxide was taken in 75 ml chilled ethanol to form a heterogeneous solution. Approximately 0.2 g octadecyldimethyl (3-trimethoxy silylpropyl) ammonium chloride was added drop wise under vigorous stirring. Then, the pH of the mixed solution was adjusted by 1(M) NaOH solution and pH of the mixed solution was fixed at 10. Finally, the mixed solution was heated at 80° C. and maintained for 2 h. The resultant mixture was autoclaved at 180° C. for 24 h for further crystallization. The white precipitate (TiO2) was collected by filtration, washed thoroughly with distilled water and ethanol and dried at 80° C. for 12 h. To remove the template the as-synthesized material was heated to 750° C. with a temperature ramp of 1.5° C. / min under static air and kept at the same temperature for 4 h. This was used as a TiO2 support material.
Synthesis of Mo—TiO2
[0075]Synthesis of Mo—TiO2 catalyst using ethanol (25 ml) medium taking the solution composition of 1....
example 2
[0077]This example describes the dehydrogenation of ethane by gas phase reaction in He using Mo—TiO2 nanocrystalline oxide as the catalyst. (Table-1)
[0078]The dehydrogenation of ethane to ethylene was carried out in a fixed-bed down flow quartz reactor at atmospheric pressure. Typically 200 mg of catalyst was placed in between two quartz wool plugged in the center of the 6 mm quartz reactor and dehydrogenation of ethane was carried out in a temperature range of 650-800° C. The gas hourly space velocity (GHSV) was varied between 10000 ml g−1 h−1 to 30000 ml g−1 h−1 with a molar ratio of C2H6:He of 1:9.
[0079]Process Conditions
Catalyst: 0.2 g
[0080]Mo: TiO2 wt % in the catalyst=5%
Pressure: 1 atmosphere
Total flow=33.3 ml / min (GHSV=10000)
Reaction time: 1 h
TABLE 1EthaneEthyleneCatalystTemperatureConversionSelectivityYield(5% Mo—TiO2)(° C.)(mol %)(mol %)(%)Oxidative750918476dehydrogenation (WithO2)dehydrogenation750869582(Without O2)
example — 3
Example—3
[0081]The example describes the effect of temperature on yield and selectivity ethylene. The product analysis presented in Table-2.
[0082]Process Conditions:
Catalyst: 0.2 g
[0083]Mo: TiO2 wt % in the catalyst=5%
Pressure: 1 atmosphere
Total flow=33.3 ml / min (GHSV=10000)
Reaction time: 1 h
TABLE 2Effect of temperature on ethane conversion, ethylene yield and selectivityEthaneEthyleneTemperatureConversionSelectivity (molYield(° C.)(mol %)%)(%)Oxidative650658958dehydrogenation700828771(With O2)750918476800967874dehydrogenation6501010010(Without700569754O2)750869582800948984
PUM
Property | Measurement | Unit |
---|---|---|
Temperature | aaaaa | aaaaa |
Temperature | aaaaa | aaaaa |
Temperature | aaaaa | aaaaa |
Abstract
Description
Claims
Application Information
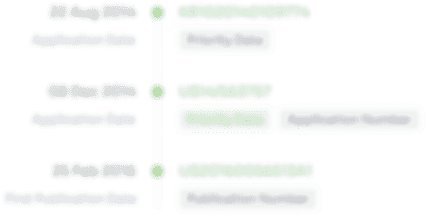
- R&D Engineer
- R&D Manager
- IP Professional
- Industry Leading Data Capabilities
- Powerful AI technology
- Patent DNA Extraction
Browse by: Latest US Patents, China's latest patents, Technical Efficacy Thesaurus, Application Domain, Technology Topic.
© 2024 PatSnap. All rights reserved.Legal|Privacy policy|Modern Slavery Act Transparency Statement|Sitemap