Sputter etch processing for heavy metal patterning in integrated circuits
a technology of integrated circuits and etching profiles, which is applied in the direction of semiconductor devices, semiconductor/solid-state device details, electrical apparatus, etc., can solve the problems of reentrant reactive ion etching profiles, poor liner/seed coverage on the walls of trenches, and damascene processing that is not always compatible with the trend toward smaller feature sizes
- Summary
- Abstract
- Description
- Claims
- Application Information
AI Technical Summary
Benefits of technology
Problems solved by technology
Method used
Image
Examples
Embodiment Construction
[0011]In one embodiment, the invention is a method and apparatus for heavy metal patterning using a sputter etch process. Embodiments of the invention pattern fine metal lines on an insulating layer of an integrated circuit via a subtractive process (i.e., a process that creates a desired structure by removing material rather than by adding material). In a particular embodiment, the subtractive process uses chlorine and fluorine etch chemistry in a two-step process to control the patterning of hard masks on copper containing conductive metal. In particular, the disclosed process allows for easier control of the hard mask profile during subtractive copper and copper alloy etching, as well as easier control of the copper patterning.
[0012]FIGS. 2A-2J are schematic diagrams illustrating various stages of fabrication of a complementary metal-oxide-semiconductor (CMOS) device 200, according to embodiments of the present invention. As such, FIGS. 2A-2J also collectively serve as a flow diagra
PUM
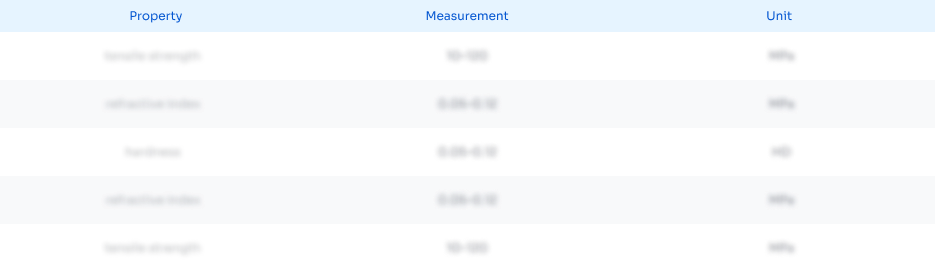
Abstract
Description
Claims
Application Information
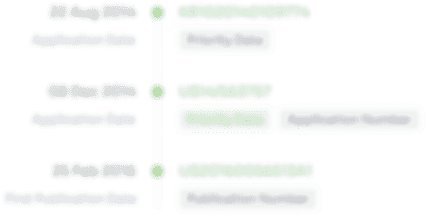
- R&D Engineer
- R&D Manager
- IP Professional
- Industry Leading Data Capabilities
- Powerful AI technology
- Patent DNA Extraction
Browse by: Latest US Patents, China's latest patents, Technical Efficacy Thesaurus, Application Domain, Technology Topic.
© 2024 PatSnap. All rights reserved.Legal|Privacy policy|Modern Slavery Act Transparency Statement|Sitemap