Preparation method for catalyst for preparing chloroethylene via ethane oxychlorination
A technology for producing vinyl chloride and catalysts by oxychlorination of ethane, which is applied in the field of preparation of catalysts for producing vinyl chloride by oxychlorination of ethane, can solve problems such as affecting the service life of catalysts, reducing catalyst activity, and loss of Fe ions, so as to reduce energy consumption. Consumption, good catalytic activity, low cost effect
- Summary
- Abstract
- Description
- Claims
- Application Information
AI Technical Summary
Benefits of technology
Problems solved by technology
Method used
Image
Examples
Embodiment 1
[0015] Embodiment 1: 1.19g tin powder is dissolved in 50ml dilute cold nitric acid and is made into tin nitrate solution, takes by weighing 4.34g cerium nitrate hexahydrate, 0.5g potassium nitrate, 4.04g ferric nitrate nonahydrate, 12.5g citric acid monohydrate, Add 0.3g of polyethylene glycol 2000 and 5.2g of titanium dioxide into the tin nitrate solution, then add 30ml of deionized water, stir and evaporate the water in a water bath at 80°C, dry at 100°C for 14h, then bake at 500°C for 3h, and then bake at 700°C for 3h A catalyst for producing vinyl chloride by oxychlorination of ethane is obtained.
Embodiment 2
[0016] Embodiment 2: 0.59g tin powder is dissolved in 50ml dilute cold nitric acid and is made into tin nitrate solution, takes by weighing 2.17g cerium nitrate hexahydrate, 0.5g potassium nitrate, 2.02g ferric nitrate nonahydrate, 12.5g citric acid monohydrate, Add 0.3g of polyethylene glycol 2000 and 6.4g of titanium dioxide into the tin nitrate solution, then add 30ml of deionized water, stir and evaporate the water in a water bath at 80°C, dry at 100°C for 14h, then bake at 500°C for 3h, and then bake at 700°C for 3h A catalyst for producing vinyl chloride by oxychlorination of ethane is obtained.
Embodiment 3
[0017] Embodiment 3: 0.59g tin powder is dissolved in 50ml dilute cold nitric acid and is made into tin nitrate solution, takes by weighing 4.34g cerium nitrate hexahydrate, 0.5g potassium nitrate, 2.78g ferrous sulfate heptahydrate, 12.5g citric acid monohydrate , 0.3g of polyethylene glycol 2000 and 5.2g of titanium dioxide were added to the tin nitrate solution, and then 30ml of deionized water was added, stirred and evaporated in a water bath at 80°C, dried at 100°C for 14h, then calcined at 500°C for 3h, and then calcined at 700°C 3h to obtain a catalyst for the production of vinyl chloride by oxychlorination of ethane.
PUM
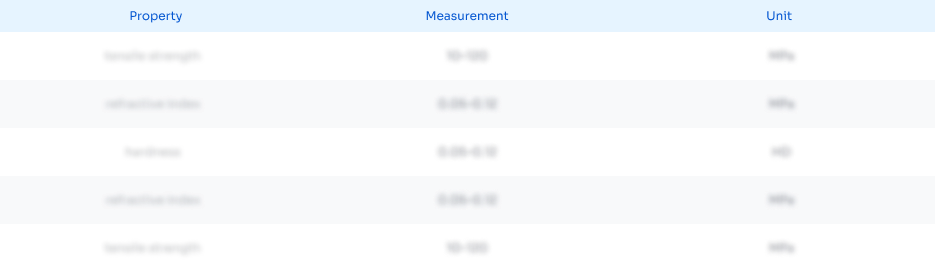
Abstract
Description
Claims
Application Information
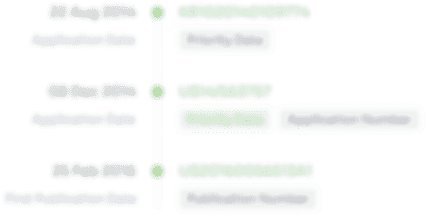
- R&D Engineer
- R&D Manager
- IP Professional
- Industry Leading Data Capabilities
- Powerful AI technology
- Patent DNA Extraction
Browse by: Latest US Patents, China's latest patents, Technical Efficacy Thesaurus, Application Domain, Technology Topic.
© 2024 PatSnap. All rights reserved.Legal|Privacy policy|Modern Slavery Act Transparency Statement|Sitemap