Device and method for improving finishing temperature of oriented silicon steel
A technology of final rolling temperature and oriented silicon steel, which is applied in metal rolling and other directions, can solve the problem of high investment, achieve the effects of reducing heat conduction, improving the uniformity of lateral distribution, and reducing the failure rate of magnetic properties
- Summary
- Abstract
- Description
- Claims
- Application Information
AI Technical Summary
Problems solved by technology
Method used
Image
Examples
Example Embodiment
[0020] The specific embodiments of the present invention will be described in detail below with reference to the accompanying drawings and embodiments, but the specific embodiments of the present invention are not limited to the following embodiments.
[0021] Device embodiment
[0022] For the structure of this embodiment, see figure 1 , figure 2 and image 3 , it is on the two hot rolling mill rails 5 of the ¢450×350mm two-roll reversible rapid hot rolling mill, along the hot rolling mill rail 5, fasten the steel template 1 as the support plate of the asbestos plate 2 of the heat insulation board, the steel The two sides of the template 1 are folded down into side plates 7, and the flat plate 8 is covered on the top of the two hot rolling mill rails 5, and the two hot rolling mill rails 5 are clamped between the two side plates 7. The two ends are bent down to form baffles 6, each end has two baffles 6, and each hot rolling mill rail 5 has a baffle 6 at both ends, a
PUM
Property | Measurement | Unit |
---|---|---|
Thickness | aaaaa | aaaaa |
Abstract
Description
Claims
Application Information
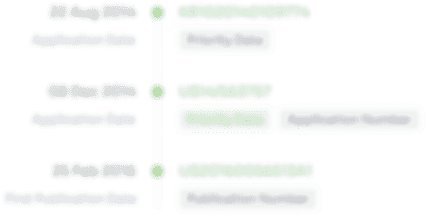
- R&D Engineer
- R&D Manager
- IP Professional
- Industry Leading Data Capabilities
- Powerful AI technology
- Patent DNA Extraction
Browse by: Latest US Patents, China's latest patents, Technical Efficacy Thesaurus, Application Domain, Technology Topic.
© 2024 PatSnap. All rights reserved.Legal|Privacy policy|Modern Slavery Act Transparency Statement|Sitemap